Surface Finishing Services
Elevate both the performance and visual appeal of your CNC-machined parts with our precision surface finishing capabilities. From deburring and polishing to anodizing, plating, and coating, we apply the right finish to improve wear resistance, corrosion protection, and dimensional accuracy—tailored to your specific application and industry standards.
NDA available upon request before quoting.
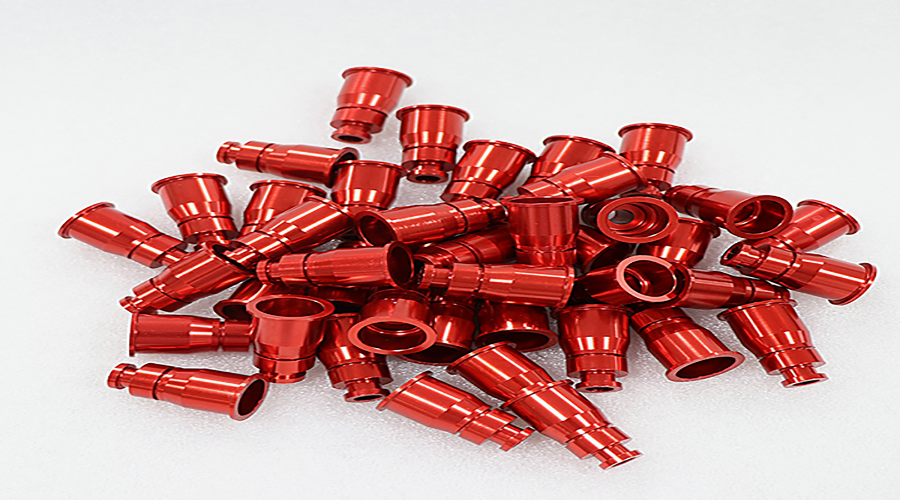
Refined Benefits of the Metal Finishing Process
– Achieving a uniform, professional surface appearance
– Enhancing corrosion, chemical, and wear resistance for demanding environments
– Improving dimensional precision and tolerance control
– Reducing surface friction and removing machining burrs
– Enabling tight adhesion for secondary coatings or paints
– Serving as a base for aesthetic finishes or protective layers
– Ensuring product longevity while meeting industry-specific standards
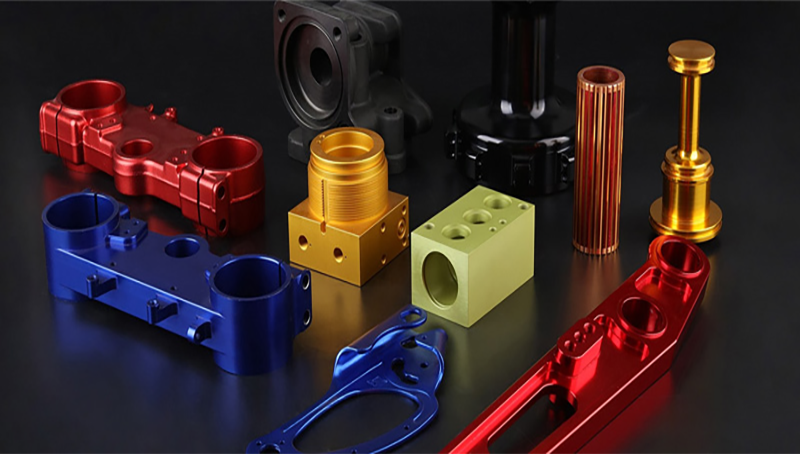
What Is the Metal Finishing Process & How Does It Work?
Metal finishing is a critical post-machining process in precision manufacturing that enhances the performance, durability, and aesthetics of CNC-machined components. This process involves applying various surface treatment techniques—such as plating, anodizing, polishing, or coating—to alter and improve the part’s exterior characteristics. By adding a metallic or non-metallic layer to the surface, metal finishing provides improved corrosion and chemical resistance, increased hardness and wear resistance, and refined electrical conductivity. It also removes burrs, corrects minor surface imperfections, and allows for custom visual finishes including color matching and gloss control. Our surface finishing services are widely applied to high-precision CNC parts made from aluminum, stainless steel, brass, and other metals—ensuring each part not only performs at peak levels but also looks its best. With First Mold, your parts aren’t just manufactured—they’re perfected.
Different Types of Metal Finishes – Metal Surface Finishing Services Available
Anodizing
Anodizing is an electrolytic surface treatment that enhances the natural oxide layer on CNC-machined metal parts, forming a uniform, controlled coating that significantly improves corrosion resistance, surface hardness, and wear performance. This process also enables aesthetic customization through color anodizing. While aluminum remains the primary substrate due to its excellent anodizing characteristics, the process is also applicable to metals such as stainless steel, titanium, copper, zinc, and magnesium
Electroplating
Electroplating is an electrochemical surface finishing process that deposits a uniform metallic coating onto CNC-machined parts by reducing metal ions from a solution onto the component’s conductive surface. This method is commonly used to enhance surface hardness, improve corrosion and wear resistance, increase dimensional accuracy for undersized features, popular electroplating options include chrome plating, nickel plating, and other specialized coatings tailored to functional and visual performance requirements.
Polishing
Polishing is a surface refinement process that involves mechanical abrasion or chemical treatment to achieve a smooth, mirror-like finish on CNC machined parts. This technique enhances the part’s surface by minimizing micro-defects, reducing surface roughness, and improving reflectivity—making it ideal for components that require both aesthetic appeal and functional performance, such as in optical, medical, and high-end consumer applications.
Powder Coating
Powder coating is an advanced dry finishing process where finely ground particles of pigment and resin are electrostatically charged and sprayed onto a grounded CNC-machined component. The coated parts are then cured under high temperature, allowing the powder to melt, flow, and form a uniform, hard-wearing finish.
Abrasive blasting (Sandblasting)
Abrasive blasting—commonly known as sandblasting—is a surface finishing process that involves propelling high-velocity abrasive particles (typically aluminum oxide, garnet, or glass beads) against a metal surface using a pressurized air or mechanical blasting system. This controlled erosion technique effectively removes oxidation, scale, and other surface contaminants,
Black Oxide (Hot Blackening)
Black oxide treatment—also referred to as blackening or gun bluing—is a chemical conversion process that creates a thin, uniform black oxide layer on the surface of ferrous metals, stainless steel, copper and copper alloys, zinc, powdered metals, and silver solder. This conversion coating is achieved through a controlled oxidation reaction that forms magnetite (Fe₃O₄) on the surface. The resulting finish enhances corrosion resistance reduces glare and light reflection,