High-Accuracy CNC Machining Solutions with Rigorous Quality Assurance
Our CNC precision machining service exceeds standard processes by employing state-of-the-art machining centers combined with advanced surface-polishing systems to deliver unrivaled detail and finish quality.
NDA available upon request before quoting.
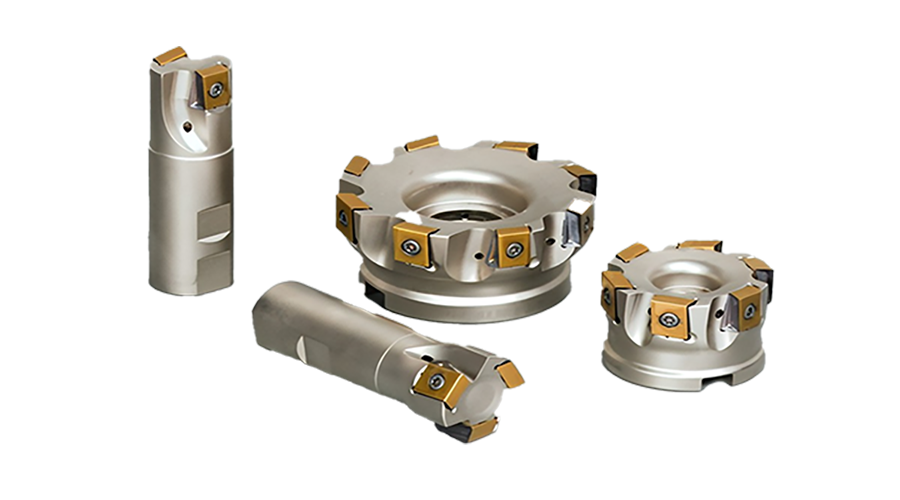
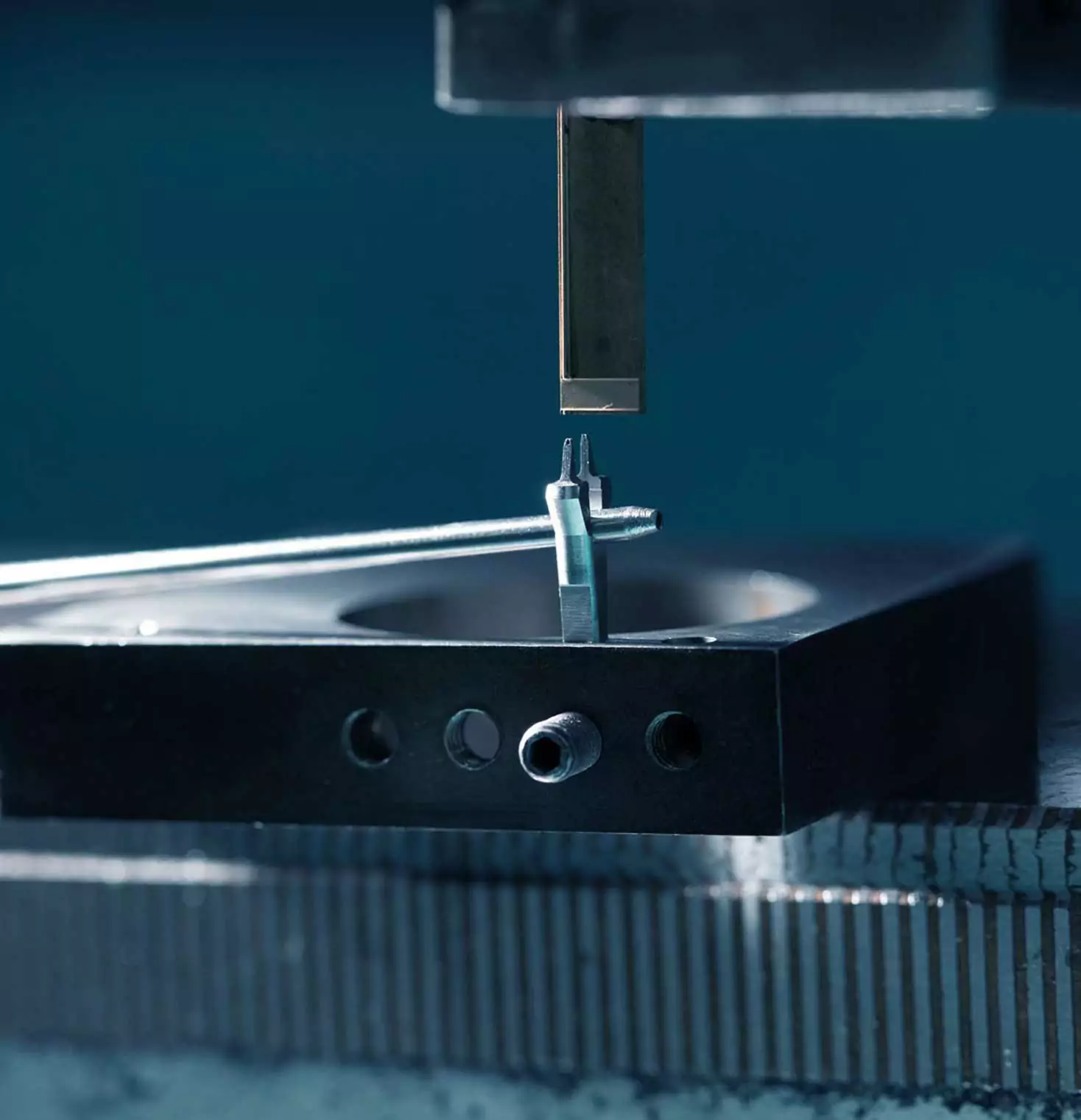
Supplying flexible solutions to meet your rapid prototyping needs.
With a fleet of over 40 advanced CNC milling machines—including 3-axis, 4-axis, and 5-axis configurations—we deliver high-precision prototypes and low-volume production parts with exceptional speed, accuracy, and repeatability. Our capabilities allow us to tackle even the most intricate geometries and ensure optimal functionality in every part produced.
CNC milling is particularly well-suited for components featuring flat surfaces, angled cuts, slots, grooves, and complex contours. It also plays a critical role in secondary operations, such as refining details on turned, molded, or 3D-printed parts.
Tailored CNC Milling for Diverse Industrial Applications
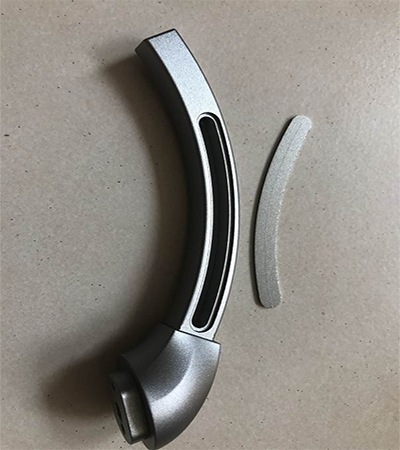
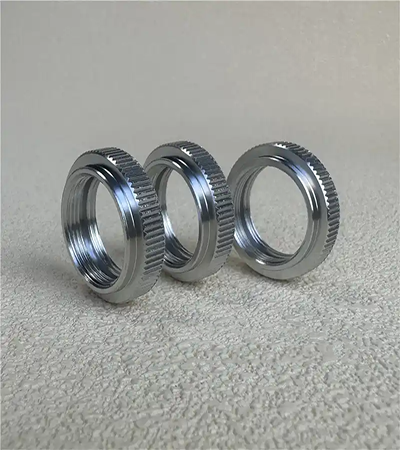
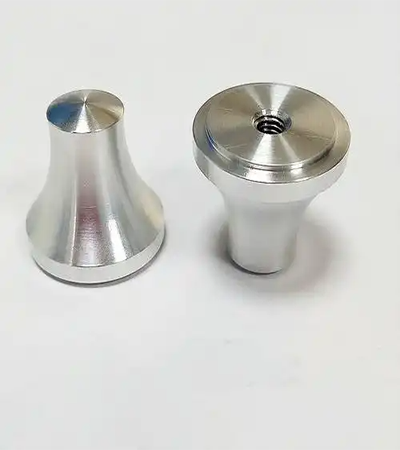
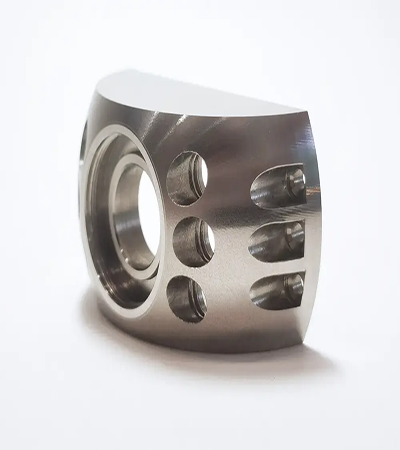
At Mazaro,We understand that delivering flawless components is critical to your success. That’s why our CNC machining specialists combine decades of hands‑on experience with a rigorous ISO 9001‑certified quality management system to ensure precision, efficiency, and repeatability at every stage of production. Whether your project calls for simple brackets or intricate aerospace fittings—in volumes from prototypes to full production runs—each part undergoes comprehensive inspection using state‑of‑the‑art metrology: CMM, 2D measuring instruments, XRF analyzers, pin gauges, micrometers, and calipers. From initial sample to final shipment, we monitor dimensional accuracy and functional performance, and we implement immediate corrective actions at the first sign of deviation. The result is consistently reliable, high‑precision parts that meet the most demanding tolerances of today’s competitive manufacturing landscape.
Advanced 5‑Axis CNC Machining Solutions – High‑Precision Manufacturing with State‑of‑the‑Art Five‑Axis Centers
As a seasoned CNC machine shop, Junying delivers precision 5‑axis machining for metal and plastic components to clients worldwide.
Leveraging advanced five‑axis centers and expert CAM programming, we tackle the most complex geometries with tight tolerances and superior surface finishes.
Serving automotive, aerospace, medical, defense, and high‑tech sectors, our rigorous process control and proactive problem‑solving ensure consistent quality and on‑time delivery.
Choose Junying for a cost‑effective, reliable partner that transforms your most demanding CNC projects into high‑performance solutions.
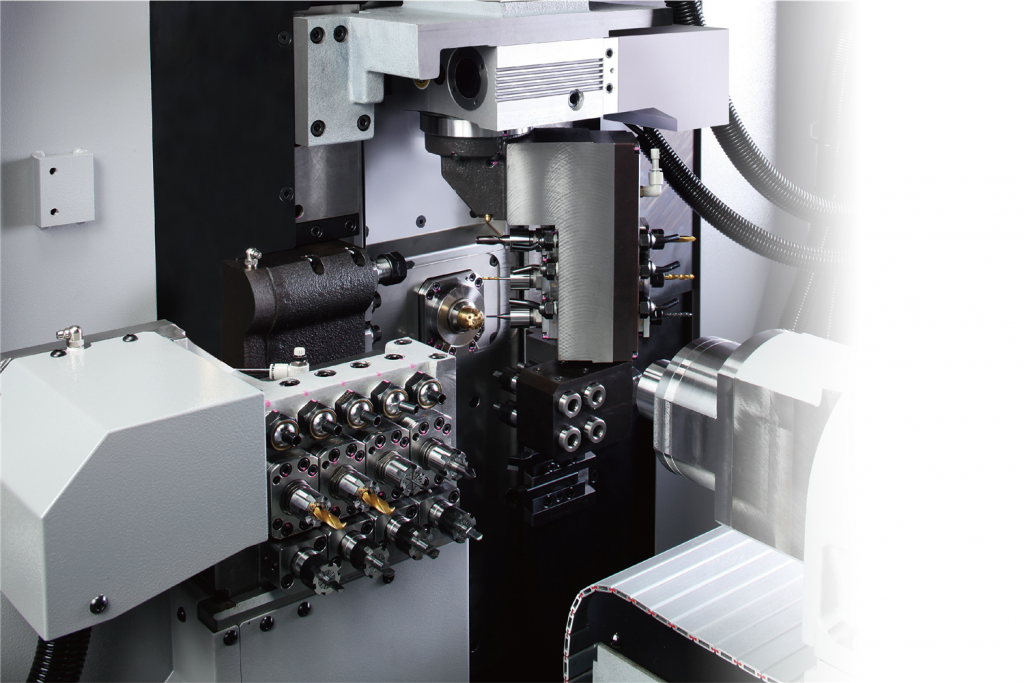
Overview of Milling Cutters & Cutting Tools in CNC Milling
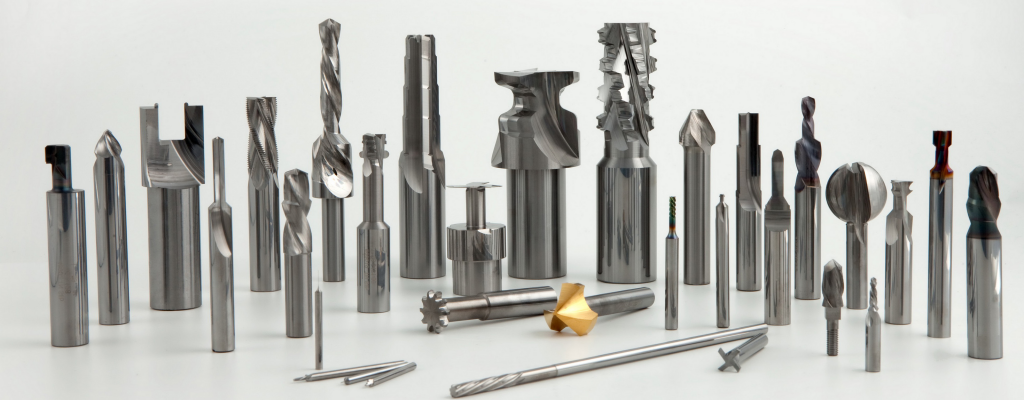
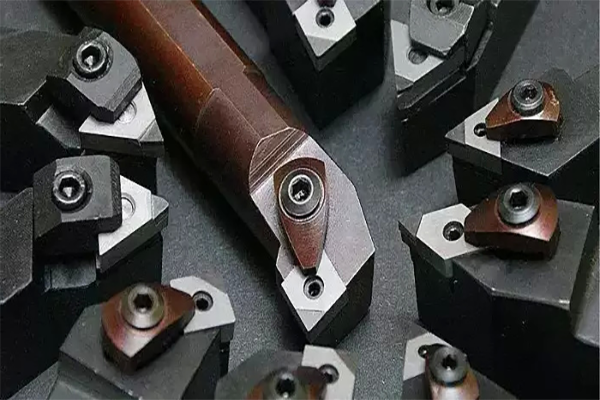

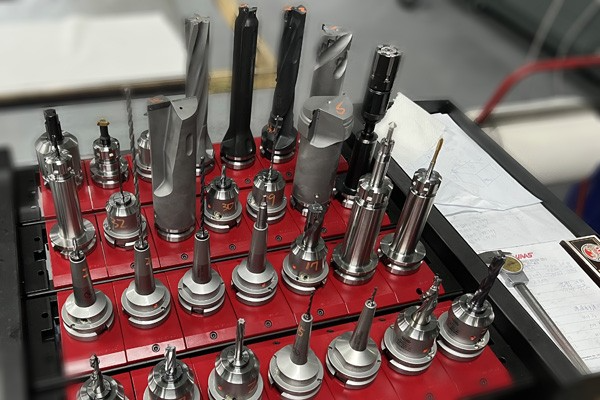
Understanding CNC Milling: Defining CNC Mills and Exploring Machine Variations
Our CNC mills use high‑speed spindles and precision milling cutters to carve complex slots, holes, pockets, and profiles. Featuring multi‑axis control, they execute angular cuts and 3D contours in a single setup, while programmable worktable movements guarantee repeatable positioning. Ideal for both prototypes and production runs, CNC milling delivers versatile geometries with exceptional accuracy and efficiency.
• 3‑Axis Mills: Standard XYZ travel enables vertical and lateral cuts with rapid setup, ideal for straightforward parts and high-speed production.
• 4‑Axis Mills: Adding a rotary B‑axis lets the cutter index around the workpiece, reducing setups and unlocking helical slots, side milling, and drilling at compound angles.
• 5‑Axis Mills: Two rotary axes deliver full simultaneous motion, enabling single‑setup machining of complex 3D contours, undercuts, and intricate geometries with unmatched accuracy and efficiency.
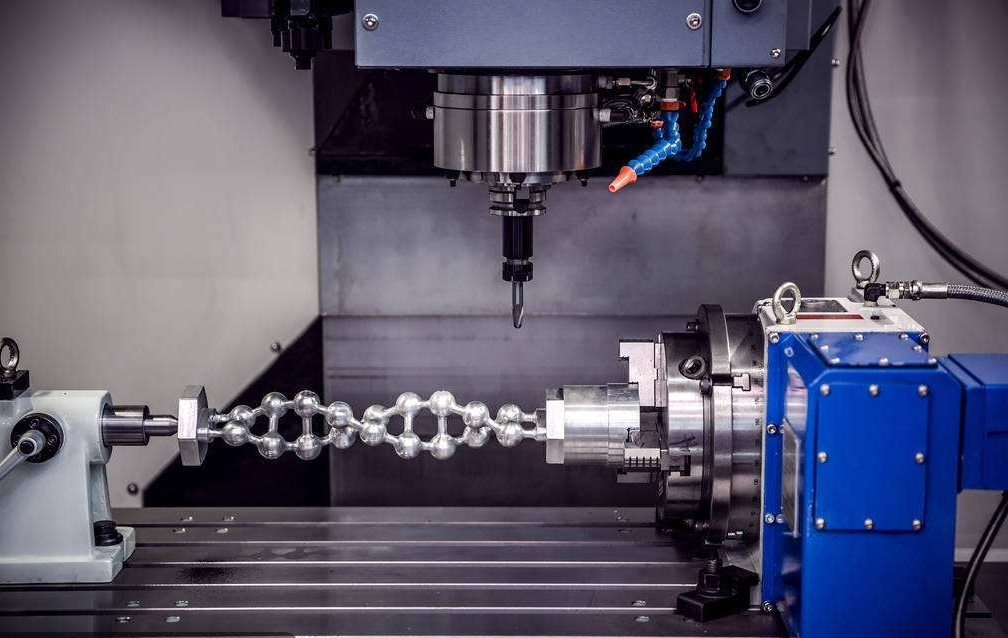
CNC Milling Tooling: Types of Cutters & Applications
Cutter Type | Description |
---|---|
End mills | The most commonly used milling cutters, with cutting edges on both the bottom and the sides, allowing them to cut in multiple directions. |
Ball nose end mills | Similar to end mills but have a rounded end, suitable for machining curved surfaces. |
Face mills | Used to cut flat surfaces and create square edges. |
Hollow mills | The opposite of face mills: the workpiece is fed into the inner part of the cutter to produce a cylindrical feature. |
Side‑and‑face cutters | With teeth around the circumference and one side, they function similarly to end mills. |
Fly cutters | Single‑point cutting tools that are used for light milling operations. |
T‑slot cutters | Used to create T‑shaped slots in the workpiece. |
Thread mills | Used to create internal or external threads in the workpiece. |
Chamfer mills | Used to create beveled edges or chamfers on the workpiece. |