Mold Making Service
We provide end-to-end mold solutions, encompassing design, precision manufacturing, rigorous inspection, and dependable maintenance—all in-house. With expertise in complex mold structures, we ensure fast lead times, often within 7 days. From concept to delivery and repair, our integrated services guarantee consistent quality and performance. Backed by competitive pricing, innovative processes, and operational efficiency,
NDA available upon request before quoting.
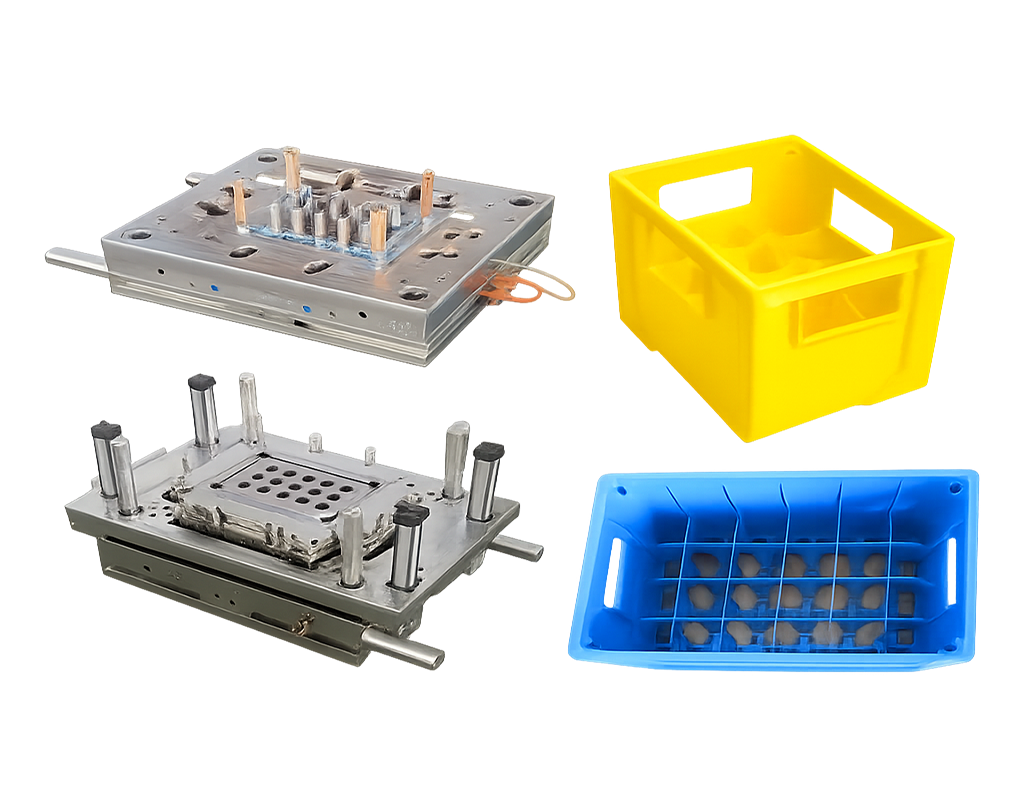
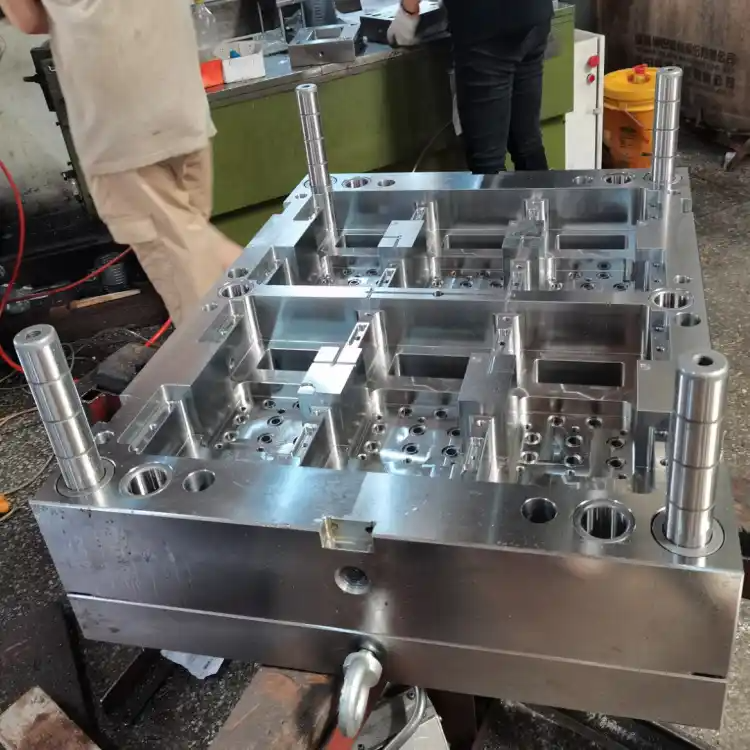
Custom Mold Solutions for Every Production Stage
Our mold offerings are tailored to meet diverse production needs. Rapid tooling enables fast turnaround times, making it ideal for small-batch and prototype production. For applications requiring tight tolerances and intricate geometries, our precision molds deliver exceptional accuracy and reliability. When it comes to medium to high-volume manufacturing, our production tooling is optimized for efficiency and consistent output, ensuring both quality and cost-effectiveness.
Comprehensive Workflow of Precision Mold Fabrication
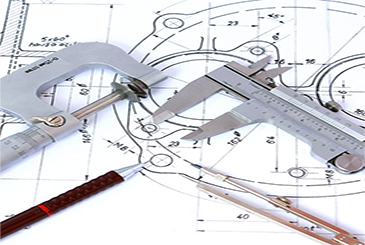
01
Initial Design & Conceptualization
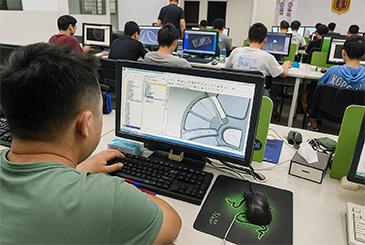
02
Detailed Mold Design and CAD Modeling
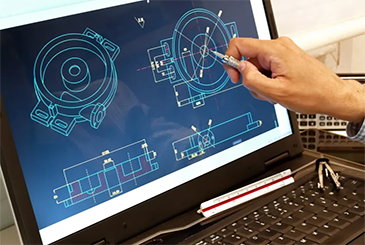
03
Simulation via Mold Flow Analysis
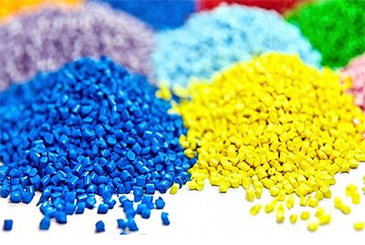
04
Selection of Optimal Mold Materials
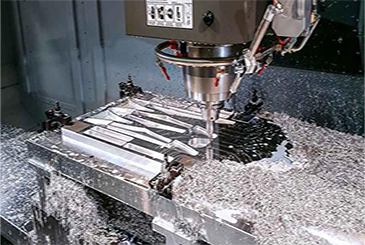
05
Fabrication of the Mold Base
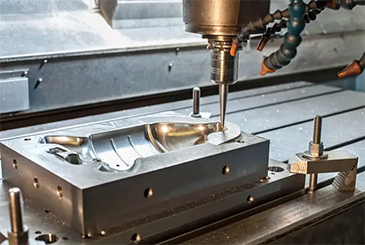
06
Precision Machining of Core and Cavity
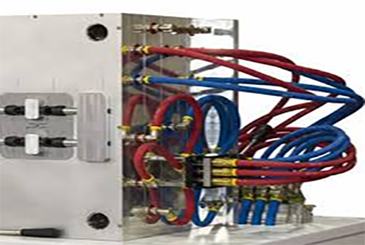
07
Design and Integration of Cooling Channels
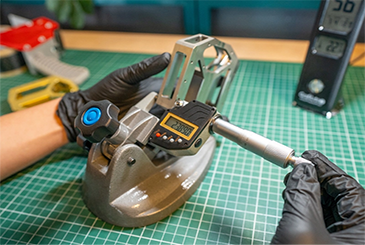
08
Installation of the Injection System
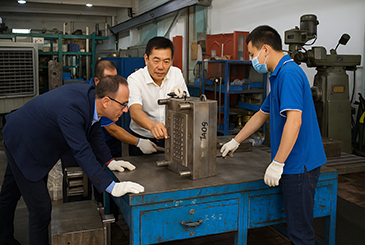
09
Assembly of All Mold Components
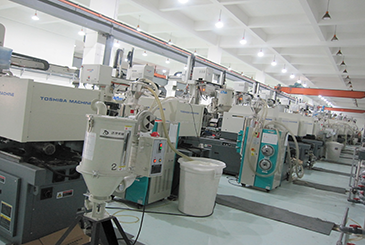
10
Trial Molding and Prototype Validation
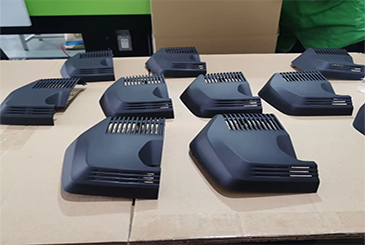
11
Fine-Tuning and Dimensional Adjustments
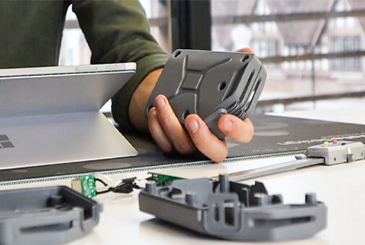
12
Final Quality Inspection and Mold Delivery
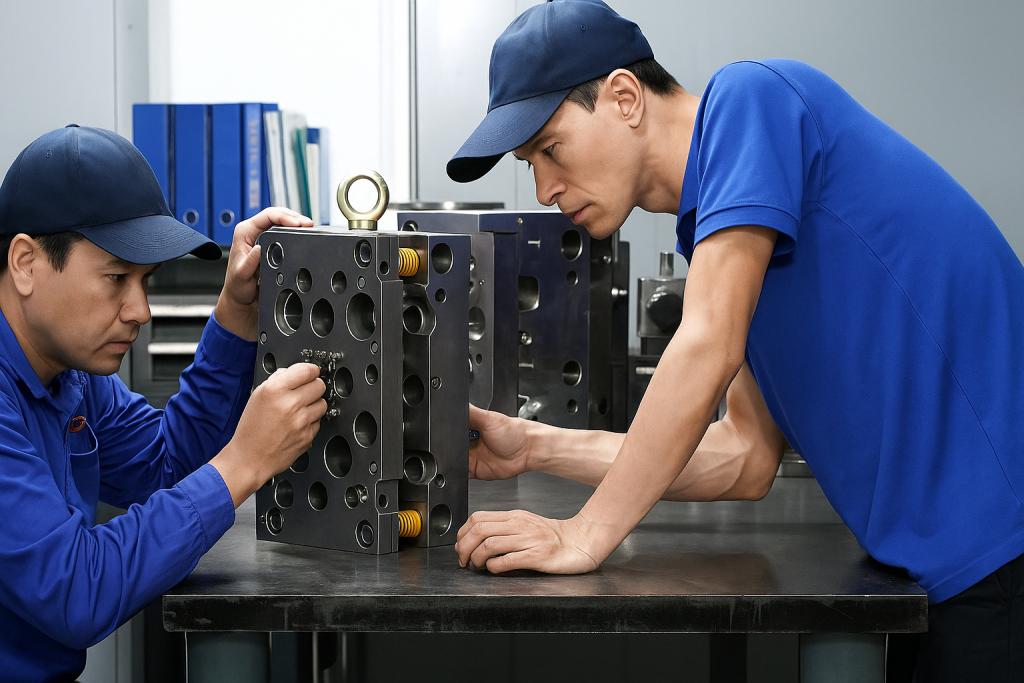
In the context of mold manufacturing, what are the primary mold types, and how do their tooling, material selection, and fabrication processes vary?
Mold manufacturing encompasses a broad range of mold types, including injection molds, die casting molds, stamping molds, forging molds, extrusion molds, and blow molding molds, each tailored for specific forming techniques and material properties.
Injection molds are designed for producing high-precision plastic components. Their fabrication emphasizes CNC machining, cooling system optimization, and surface polishing to ensure part accuracy and cycle time efficiency.
Die casting molds, used for non-ferrous metal parts like aluminum or zinc, require heat-resistant tool steels and focus on surface treatment and venting design to manage thermal loads and gas evacuation during high-pressure metal injection.
Stamping molds are employed in sheet metal forming and prioritize clearance control, alignment precision, and quenching treatment to maintain dimensional accuracy and durability under repetitive high-speed operation.
Forging molds are used to form metal blanks under high pressure and temperature. Their production involves forging the die blanks, followed by multi-step machining and rigorous heat treatment to withstand mechanical stress and maintain mold integrity.
Extrusion molds, which shape continuous profiles, rely heavily on runner design and precision machining to ensure uniform material flow and avoid deformation during extrusion.
Blow molding molds are typically made of aluminum alloys for better thermal conductivity, and the process highlights mold cavity surface finish and cooling system design to form consistent hollow plastic parts.
Each mold type involves distinct tooling strategies, materials, and processing techniques, depending on factors such as molding temperature, pressure, material behavior, and production volume. These variations directly impact the mold’s performance, longevity, and the quality of the final product.
How much time should be expected for mold production, and do timelines differ depending on the type of mold?
The mold making cycle is influenced by a variety of factors, including mold complexity, dimensions, material selection, and technical requirements such as surface finish and precision tolerances. In general:
Simple and small molds (e.g., single-cavity, low-complexity structures) can often be completed within 1 to 2 weeks.
Medium-complexity molds typically require around 2 to 4 weeks, depending on features like sliders, lifters, and multi-cavity layouts.
Highly complex or large-scale molds, such as those with intricate parting lines, precision inserts, or multi-stage ejection systems, may take 3 months to 6 months or more, especially when high durability and long production lifespans are required.
There are also significant differences in production timelines across different mold types:
Injection molds generally require 2 to 6 weeks for standard applications. However, for high-precision molds involving complex geometries, tight tolerances, and multi-cavity configurations, the lead time can extend to 8 weeks or longer.
Die casting molds have stricter requirements for material hardness, heat treatment, and surface coating (e.g., nitriding or PVD). As such, small to medium-sized die casting molds typically take 3 to 6 weeks, while large or multi-slide die casting molds may require over 3 months, especially if they involve intricate core pulling systems or high-volume production readiness
What percentage of the total mold-making cost is typically attributed to material expenses? Also, which materials are recommended for their high cost-performance ratio?
In mold manufacturing, the material cost for injection molds typically accounts for approximately 20% to 30% of the total production cost. For simple and small-sized molds, material expenses tend to be closer to 20%, whereas for large, highly precise, and complex molds, this proportion can rise to 30% or more. Due to stringent performance requirements, material costs for die-casting molds generally represent 30% to 40% of the overall cost. Small die-casting molds usually incur around 30% material costs, while large, high-performance die-casting molds may exceed 40%.
Regarding injection mold materials with favorable cost-performance characteristics, P20 steel is widely favored due to its good pre-hardening condition, ease of machining, and polishing capabilities, making it well-suited for medium and small molds with standard precision requirements. Additionally, 718 steel is frequently employed for large, complex, and precision-critical injection molds; its enhanced toughness and hardenability result from nickel alloying, offering superior durability in demanding applications.
For die-casting molds, H13 steel is a prevalent choice among hot work tool steels, prized for its excellent toughness, resistance to thermal fatigue, and wear resistance, thereby delivering excellent cost efficiency. Another notable material is 3Cr2W8V steel, which combines high-temperature strength, hardness, wear resistance, and thermal stability, making it ideal for aluminum and magnesium alloy die-casting molds. Its moderate cost further enhances its appeal as a cost-effective option in mold fabrication.
Once mold manufacturing is finished, is ongoing maintenance and care support typically offered? Additionally, how significant are the costs associated with maintaining and caring for the mold?
After the completion of mold manufacturing, professional mold manufacturers typically provide comprehensive guidance on follow-up maintenance and care. This includes instructions on routine cleaning, lubrication, rust prevention, and specific precautions tailored to different mold types. The cost associated with mold maintenance and care can vary significantly depending on various factors such as mold size, complexity, frequency of use, and the working environment.
Routine maintenance generally incurs relatively low expenses. Costs for consumables such as cleaning agents and lubricants typically range from a few dozen to several hundred dollars per session. For scheduled maintenance, simple and small molds may require a service cost of several hundred to around one or two thousand dollars per visit. In contrast, large and complex molds—such as injection or die-casting molds—may incur costs from several thousand to tens of thousands of dollars per session due to the precision and time required.
In cases where the mold experiences functional failure or damage, repair costs can be highly variable. Minor repairs may range from a few hundred to a few thousand dollars, whereas severe damage could result in expenses reaching tens of thousands of dollars or more. Such issues not only increase direct maintenance costs but may also lead to production delays and additional indirect expenses.
What factors should be mainly considered when designing molds for ABS injection molding to ensure the smooth demolding and good formation of products?
Mold manufacturing for specialized industries such as medical and aerospace involves a wide range of stringent quality standards and mandatory certification requirements to ensure product safety, reliability, and regulatory compliance.
In the medical industry, mold design and manufacturing must adhere to extremely high quality standards. Materials selected must be non-toxic, environmentally friendly, hypoallergenic, and exhibit excellent biocompatibility to prevent adverse biological responses. Dimensional accuracy is critical, with tolerances typically controlled within ±0.005 mm or even tighter, depending on the application. Furthermore, the molds must demonstrate exceptional reliability and consistency to meet the demanding standards of medical device production.
From a certification standpoint, ISO 13485 certification is essential, as it establishes a robust quality management system specifically for medical device manufacturing. Biocompatibility testing is required to ensure that materials do not pose risks to human health. Additionally, region-specific certifications must be obtained—such as CE marking for products entering the European Union and FDA approval for those marketed in the United States.
In the aerospace sector, molds must meet rigorous performance criteria. Materials must feature high strength, hardness, and toughness, along with excellent fatigue resistance and stability under extreme environmental conditions. Dimensional precision requirements are typically at the micron level, and surface finishes must be exceptionally smooth to reduce wear and enhance performance. Durability and reliability over long service lifespans are also key concerns.
Regarding certifications, compliance with the AS9100 series is mandatory, as it governs aerospace quality management systems. Special manufacturing processes—such as high-precision machining or heat treatment—require additional process-specific certifications to verify their consistency and reliability. Moreover, mold manufacturers must undergo comprehensive supplier qualification assessments, covering aspects such as technical expertise, advanced equipment, process control, and quality management systems. Only by fulfilling these stringent requirements can molds be approved for use in high-stakes aerospace applications.