Mass Production Service
Through the implementation of rigorous in-process quality control protocols, lean manufacturing principles, and precision machining practices, we ensure consistency and repeatability across every batch. Our vertically integrated supply chain and continuous process optimization allow for reduced lead times and cost-effective scaling. By incorporating advanced technologies such as automated CNC cells, real-time inspection systems, and smart production workflows,
NDA available upon request before quoting.
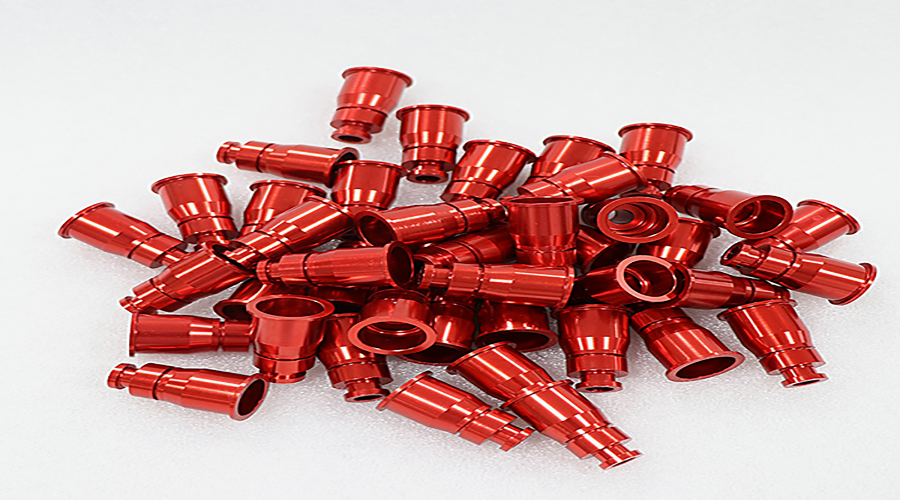
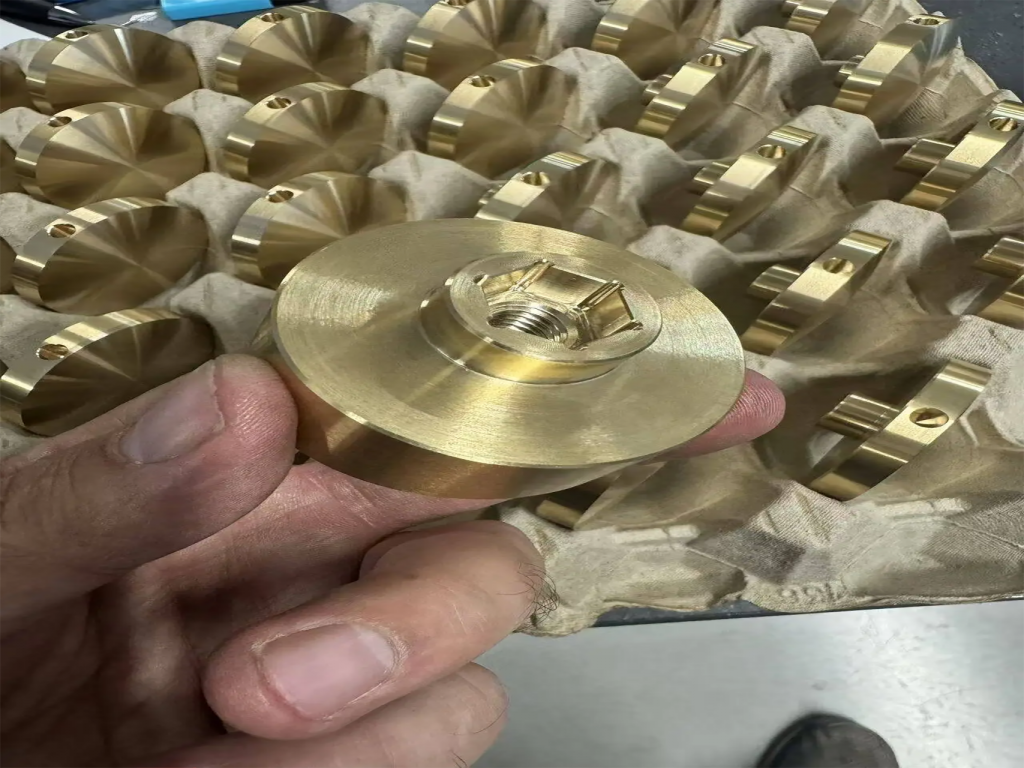
Production-Grade Mold Fabrication Capability
Precision Mold Manufacturing for High-Volume Applications
we specialize in the mass production of high-precision plastic injection molds and metal tooling systems. Leveraging advanced CNC machining centers, EDM (Electrical Discharge Machining), and automated manufacturing workflows, we are capable of delivering large-scale mold fabrication with exceptional accuracy and repeatability. Our engineering team ensures tight dimensional tolerances and robust mold construction for both complex thermoplastic components and high-durability metal parts. Serving industries including automotive, electronics, and consumer products, we provide scalable, cost-efficient, and fully optimized mold solutions tailored to high-throughput production environments.
Mass Production Showcase
Delivering Proven Solutions Across a Range of Industries
- Packaging Solutions Volume Manufacturing
- Precision instrument and timepiece component large-quantity production
- Agricultural machinery component high-volume manufacturing
- Telecommunications part mass production
- Automation system and robotics part extensive making
- Consumer electronics component extensive assembly
- Aerospace part high-volume fabrication
- Automotive interior and exterior parts production on a large scale
- Optical and photographic gear part mass fabrication
- Personal care product component volume fabrication
- Plumbing and HVAC system part mass fabrication
- Lighting and electrical component mass production
- Home appliance component bulk production
- Industrial machinery part widespread fabrication
- Energy sector component extensive production
- Medical device part large-scale manufacturing
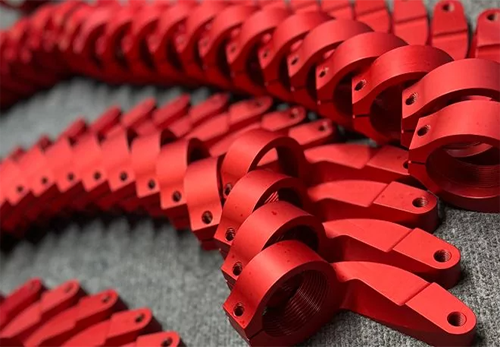
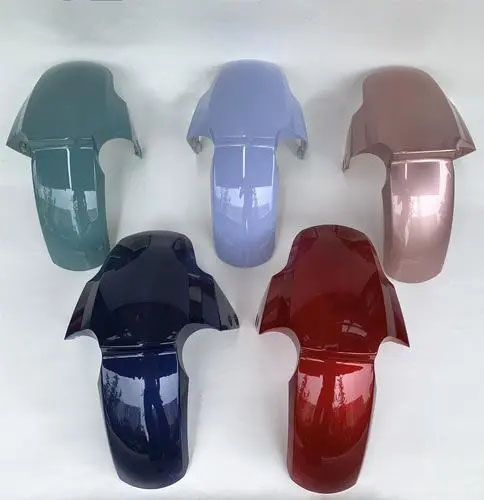
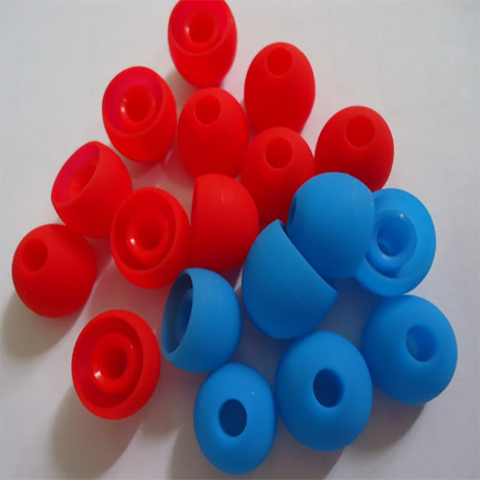
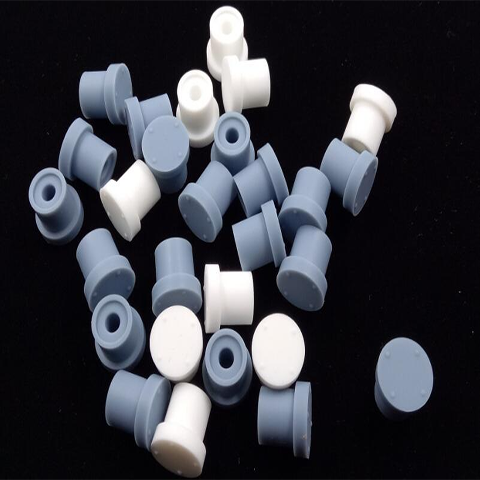
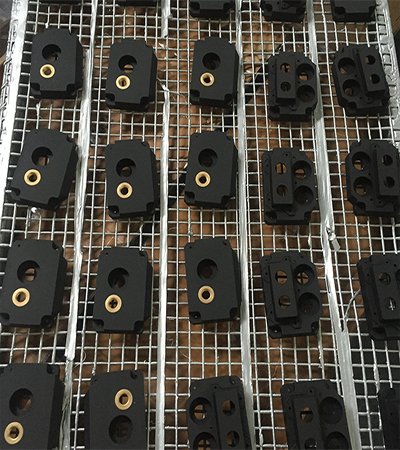
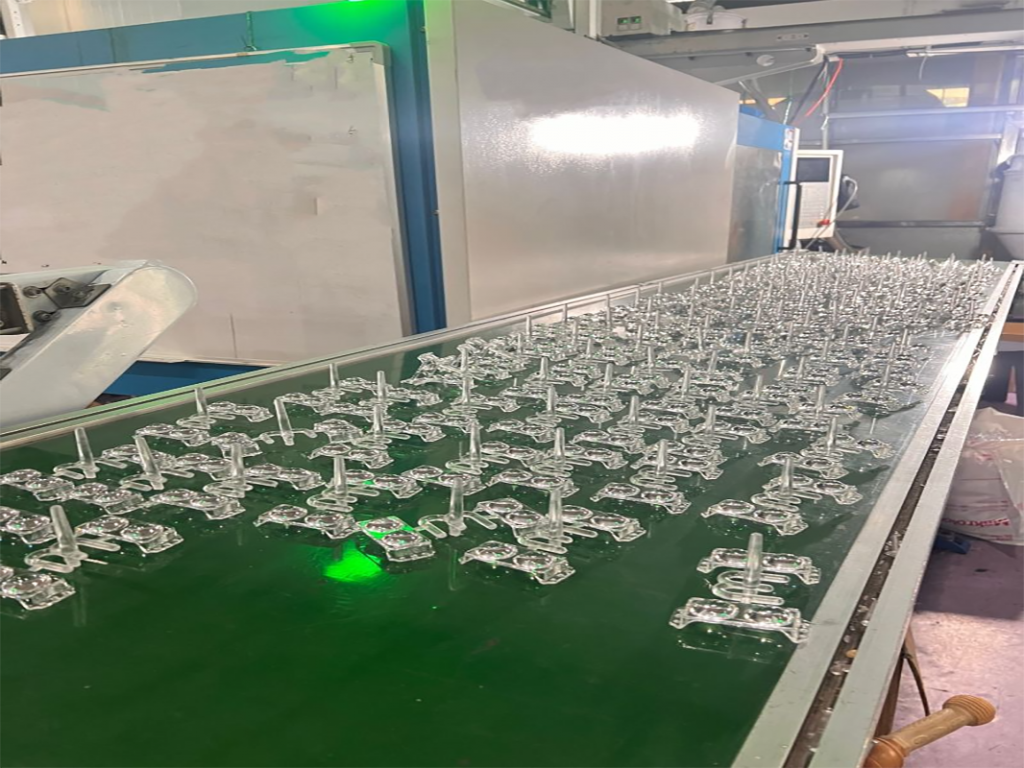
Quality Assurance in Precision Manufacturing
Quality is at the core of our CNC manufacturing process. From design to delivery, we follow strict quality standards to ensure every part meets precise specifications. Using advanced inspection tools like CMMs and applying methods such as First Article Inspection (FAI) and real-time monitoring, we guarantee consistent and reliable results. Our goal is to deliver high-quality parts that meet or exceed customer expectations every time.
- Rigorous Inspection Protocols
- State-of-the-Art Testing Equipment
- Continuous Improvement Process
Zero Surface Defects
All finished parts must be free from visual and structural defects such as burrs, flash, flow lines, sink marks, short shots, or voids. Strict inspection ensures compliance with cosmetic and structural standards
Surface Finish Quality
Surface texture and uniformity must meet defined Ra (roughness average) values as per application requirements. Surface finish affects not only appearance but also wear resistance, functionality, and bonding capability in post-processing.
Functional Testing
Each component must pass functionality validation according to design intent. This may include mechanical performance tests, fit checks, or electrical continuity tests, depending on the end-use application.
Wall Thickness Control
All molded or machined parts must maintain uniform and application-appropriate wall thickness as per design standards. Non-uniformity can lead to warpage, sink marks, or compromised strength.
Dimensional Accuracy
Critical dimensions such as length, width, height, bore diameter, and hole-to-hole spacing are verified using precision metrology tools (e.g., CMMs, micrometers, calipers) to ensure conformance to GD&T or ISO tolerances.
Environmental Reliability Testing
Products may be subjected to environmental simulation tests such as temperature cycling, humidity exposure, and vibration testing, ensuring that the part maintains mechanical and functional stability in real-world operating conditions.