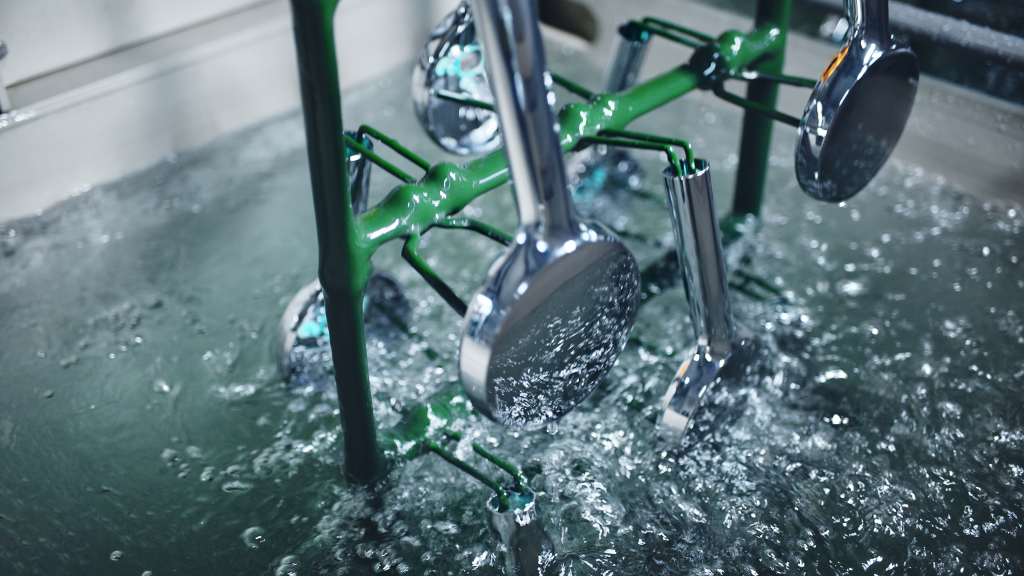
What's Electroplating?
Electroplating is a widely employed surface treatment technique applicable to both metal and plastic substrates. In this process, the workpiece to be plated is positioned as the cathode within an electrolyte bath containing dissolved metal ions, while the anode—comprising either the plating metal or an inert conductor—completes the circuit. When a direct current is applied, metal ions are reduced and deposited onto the substrate, forming a tightly bonded, uniform metal coating.This process not only enhances the visual appearance of the material but also imparts a range of beneficial physical and chemical properties, including improved corrosion and wear resistance, enhanced solderability, and tailored electrical, magnetic, and optical characteristics.
Corrosion Resistance: Depositing metals like zinc or nickel to protect the underlying material from environmental degradation.
Enhanced Aesthetics: Applying decorative finishes to improve visual appeal.
Wear Resistance: Utilizing hard metal coatings to increase surface durability.
Solderability: Improving the ability to form reliable solder joints, essential in electronics manufacturing.
Electrical Conductivity: Applying metals like copper to enhance electrical performance in components.
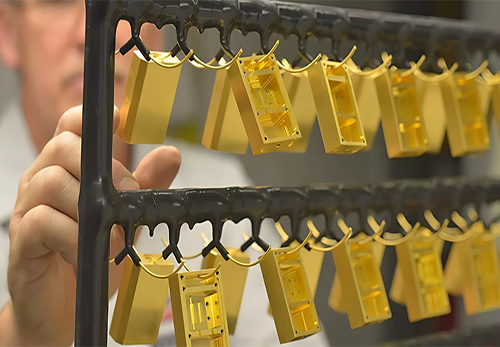
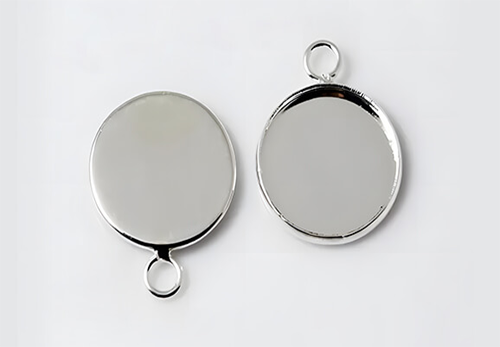
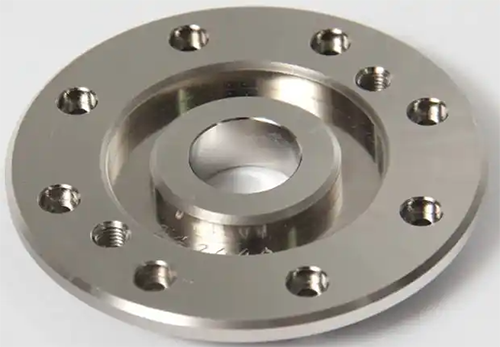
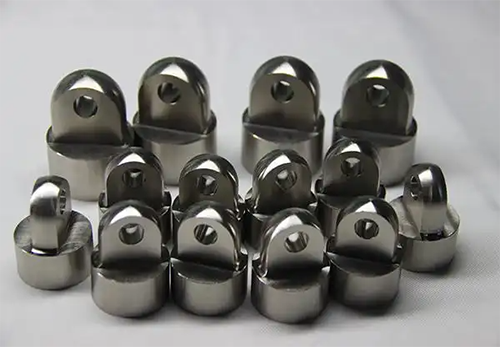
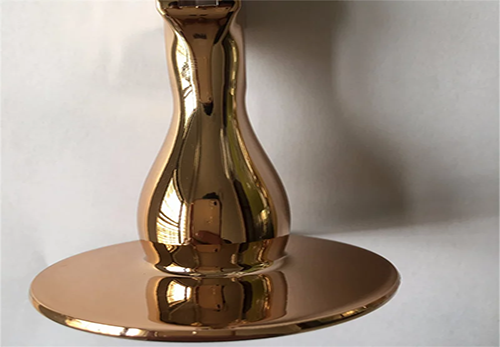
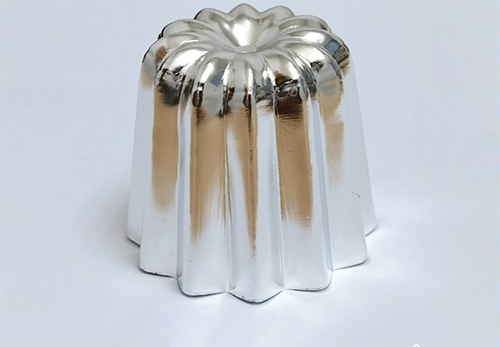
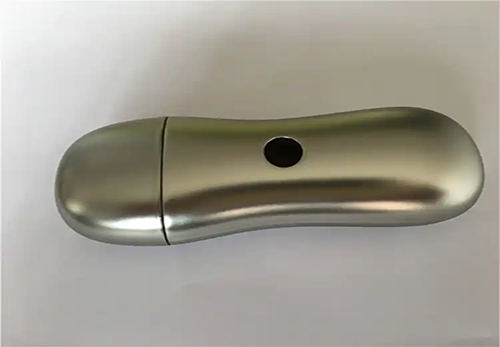
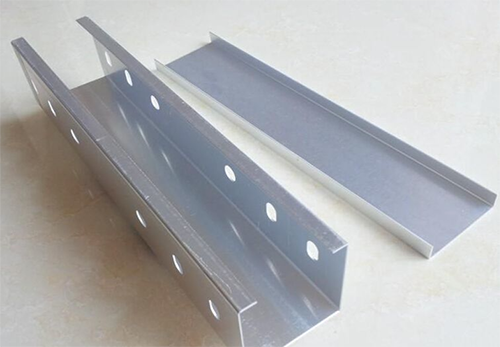
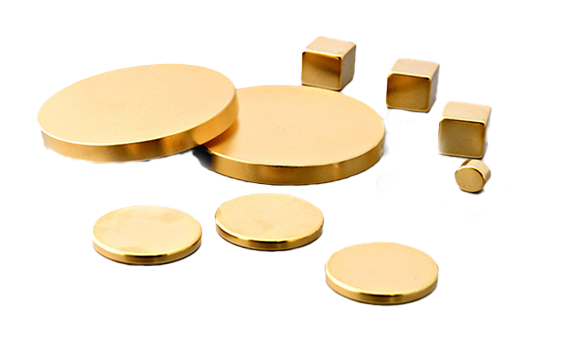
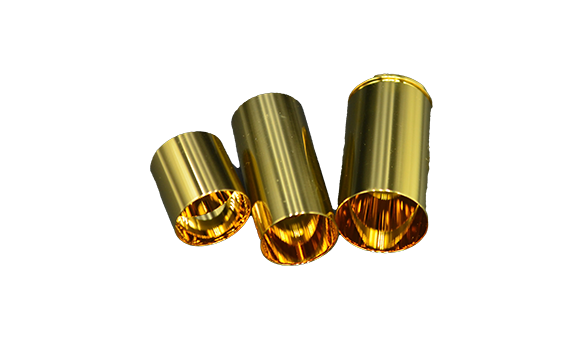
Name | Description | Material | Color | Machining Marks | Link |
---|---|---|---|---|---|
As machining | Our machined finish can be machined to Ra 3.2 μ M/Ra 126 μ Surface roughness of in and removal of sharp edges and burrs from the parts. | Metal | N/A | Slightly visible | Learn More>> |
Vapor polishing | Vapor polishing is a surface finishing technique used to improve the smoothness and clarity of a variety of materials, particularly plastics | Plastics | N/A | Smooth | Learn More>> |
Black Oxide | Black oxidation is a conversion coating used for metals. Can provide a black smooth appearance and slightly improve corrosion resistance. | Metal | Black | Visible | Learn More>> |
Alodine | Alodine, also known as chemical conversion coating or chromate conversion coating, involves applying a conversion coating solution to a metal surface, usually containing chromate compounds. | Metal | True qualities | Tool marks visible | Learn More>> |
Fine machining | Fine machining manufacturing process involves processing raw materials into parts or products with high precision, smooth surfaces, and fine size control through a series of fine machining steps. | Metals, Plastics | N/A | Slightly visible | / |
Anodizing | Anodizing process involves creating a layer of oxide on the surface of the product, which enhances its durability and resistance to corrosion. | Aluminum | Clear, black, grey, red, blue, gold | Visible under anodizing | Learn More>> |
Powder Coating | Powder coating process involves applying a dry powder to the surface of the product, which is then heated to create a smooth and durable finish. | Metal | White, Black, RAL and Pantone | Parts are powder coated directly after machining | Learn More>> |
Polishing | Polishing can create a smooth and glossy surface on the product surface. We offer different types of polishing, such as mechanical polishing and chemical polishing. | Metal | Silver gray | Removed on primary surfaces | Learn More>> |
Chromate | Chromate, commonly known as a chemical thin film, is a conversion coating used as a corrosion inhibitor on aluminum. | Aluminum | Clear/ Slight yellow tint | Machining marks are visible | Learn More>> |
Bead blasting | Bead blasting can be used to create a textured surface, remove rust or paint, or prepare a surface for further finishing. | Metal | N/A | – | Learn More>> |