Precision Forming of Corrosion-Resistant Stainless Steel Components
This process involves cutting, bending, and assembling stainless steel sheets into custom parts with high structural integrity, excellent corrosion resistance, and a clean finish—ideal for demanding applications in medical, food-grade, architectural, and industrial sectors.
NDA available upon request before quoting.
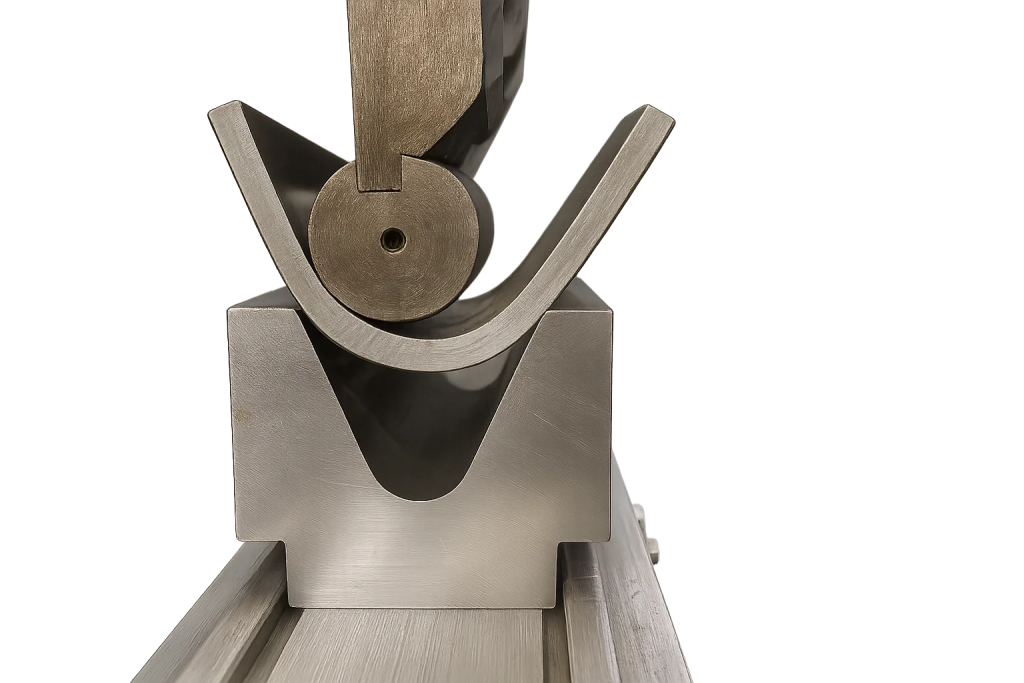
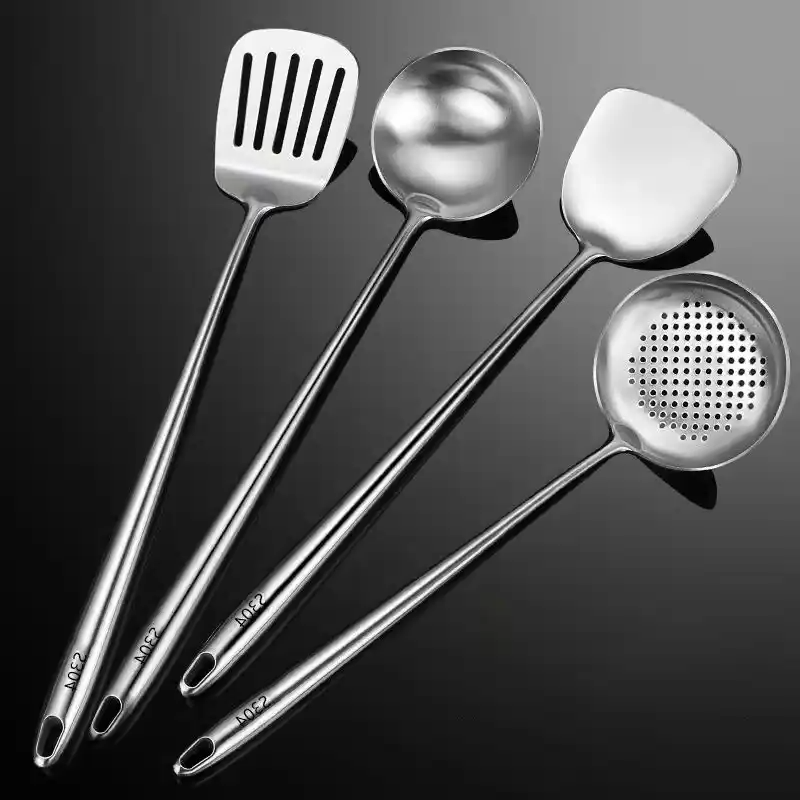
Stainless Steel Sheet Metal Manufacturing
Stainless steel stands out in sheet metal fabrication for its exceptional corrosion resistance, robust mechanical properties, and superior formability. Its durability and cost-effectiveness make it a preferred material across various industries—including automotive, architecture, construction, medical, food processing, energy, heavy industry, and chemical processing. Unlike standard steel, stainless steel resists rust, corrosion, and staining, even when exposed to harsh environments. Additionally, a range of surface treatment methods can further enhance its resistance properties. Once a stainless steel sheet is formed into a three-dimensional component, it can be finished with multiple techniques to meet specific performance and aesthetic requirements. However, not all stainless steel alloys perform identically in fabrication; selecting the appropriate grade is essential to balance cost considerations with the desired material characteristics for the intended application.
Benefits of Stainless Steel in Sheet Metal Fabrication
Superior Corrosion Resistance:
The incorporation of chromium in stainless steel imparts excellent corrosion resistance, ensuring durability in harsh environments.Versatility in Thickness:
Stainless steel sheets are available in a wide range of thicknesses, accommodating diverse design and structural requirements.Variety of Grades and Configurations:
A broad selection of stainless steel grades and configurations allows for optimal material selection tailored to specific applications.Enhanced Surface Integrity:
The manufacturing process minimizes the occurrence of stains, preserving the aesthetic quality of the finished product.Sustainability and Functional Performance:
Stainless steel is highly recyclable and exhibits strong structural integrity, good conductivity, and high reflectivity, making it a sustainable choice with multifunctional benefits.
Common Stainless Steel Grades in Sheet Metal Fabrication
Austenitic stainless steels, commonly designated as the 300 series, are highly favored in sheet metal fabrication due to their exceptional formability and ductility. Their high chromium and nickel content provides outstanding corrosion resistance, making them ideal for applications where durability is essential. Among these, SS301, SS304, and SS316 are the most frequently used grades, offering a balance of mechanical properties and corrosion resistance tailored for various industrial applications.
Stainless Steel 301:
Composition: Contains approximately 17% chromium and 7% nickel.
Mechanical Properties: Offers excellent strength and ductility, particularly during cold work.
Corrosion Resistance: Exhibits superior corrosion resistance, though slightly lower than 304/304L.
Fabrication: Highly suitable for welding, forming, and drawing operations.
Cost-Effectiveness: Serves as a less expensive alternative to 304 stainless steel.
Applications: Commonly used in structural components for trains and appliance casings.
Stainless Steel 304:
Composition: Comprises 18–20% chromium and 8–10.5% nickel.
Formability: Easily formed into various shapes, making it versatile for fabrication.
Corrosion Resistance: Resistant to a broad range of chemical corrodents, industrial environments, and marine conditions.
Magnetic Properties: May exhibit mild magnetism when worked, and it is not heat-treatable.
Applications: Widely employed in food processing equipment, such as tanks and structural bracketing.
Stainless Steel 316:
Composition: Incorporates molybdenum in addition to chromium and nickel.
Enhanced Corrosion Resistance: The presence of molybdenum improves resistance against salt water, acidic chemicals, and chlorides, making it ideal for harsh corrosive environments.
Fabrication: Maintains excellent malleability and weldability.
Applications: Commonly used for chemical tanks, maritime equipment, and other components exposed to corrosive conditions
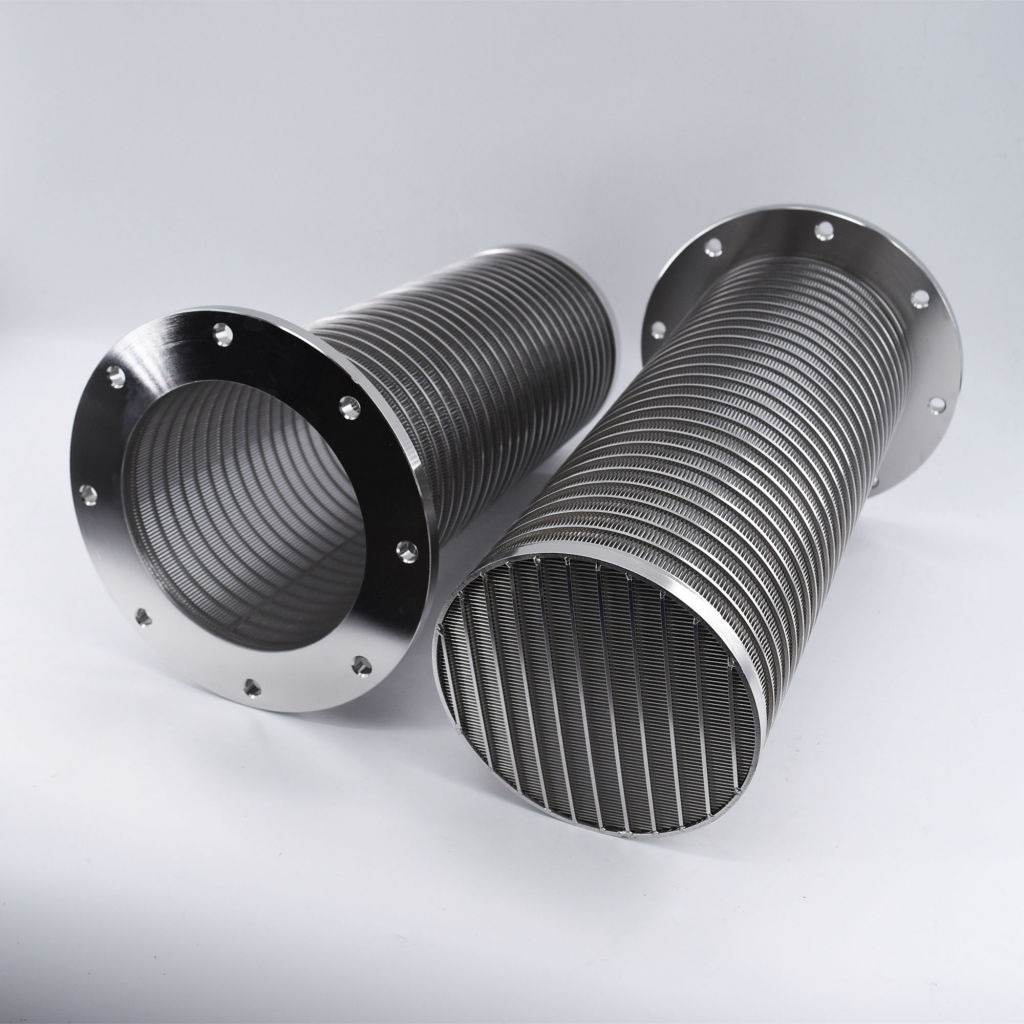