Push the boundaries of what's possible with MAZARO
Creating software and services that solve the world’s manufacturing challenges
What is CNC
CNC (Computer Numerical Control) refers to the automated control of machining tools and equipment by a computer. When a CNC system is activated, the required operations—such as cutting, milling, drilling, or turning—are programmed into specialized software. These instructions are translated into precise movements for tools and machinery, ensuring accurate execution of complex designs.
CNC programming defines the movements and tasks of a machine through a sequence of commands, known as the part program. Unlike traditional numerical control systems that relied on punch cards, CNC programs are input and managed via computer interfaces, offering greater flexibility and efficiency. The programs are stored in the computer’s memory, allowing for easy modification, updates, and the addition of new operations.
Modern CNC systems can operate multiple axes simultaneously, enabling the production of intricate parts with tight tolerances. While the software assumes precision in the machine’s mechanics, errors may arise when cutting in multiple directions simultaneously, underscoring the importance of proper calibration and tool maintenance.
CNC technology represents a significant advancement over manual machining, providing unmatched consistency, scalability, and computational power. It is the backbone of precision manufacturing, enabling the production of everything from intricate prototypes to high-volume components with exceptional accuracy.
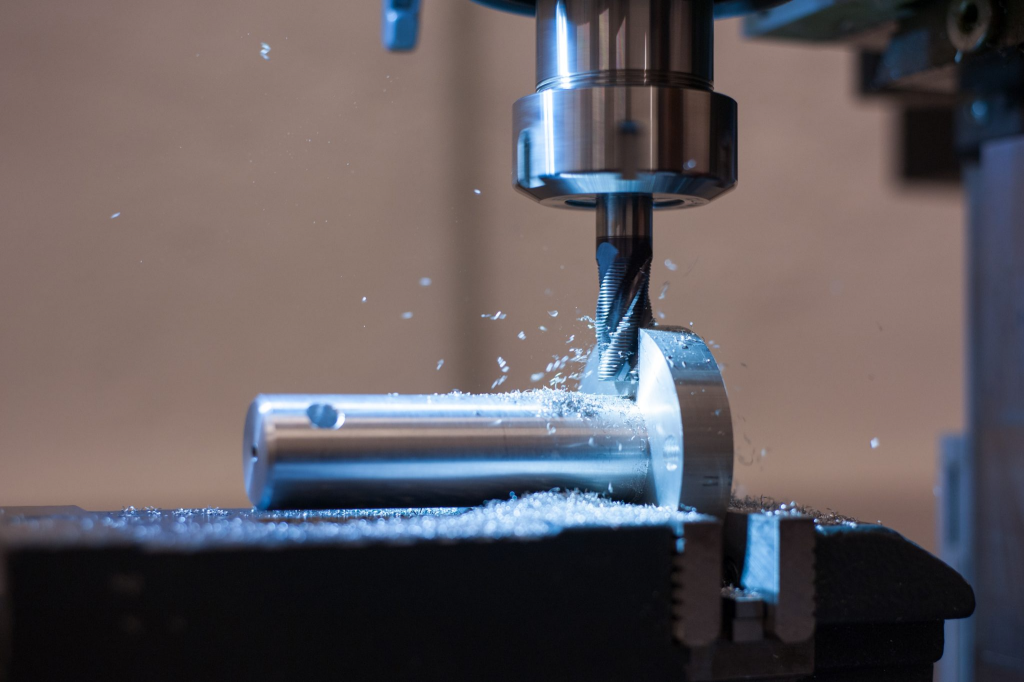
CNC Machine Programming
In CNC manufacturing, machines are controlled using numerical systems, where specialized software programs dictate the precise movements and operations of the machinery. The programming language behind CNC machining is commonly known as G-code, which governs critical machine behaviors such as speed, feed rate, and tool coordination.
CNC machining enables the pre-programming of tool movements and operations, allowing machines to execute repetitive, precise, and predictable cycles with minimal human intervention. The process begins with a 2D or 3D CAD design, which is then converted into machine-readable code for the CNC system. Before production, the program undergoes a trial run to identify and correct any errors, ensuring flawless execution during actual manufacturing.
This level of automation and precision has made CNC machining an integral part of modern manufacturing, especially in metal and plastic production. By streamlining complex processes and ensuring consistent quality, CNC programming has revolutionized industries ranging from aerospace and automotive to medical devices and consumer goods.
Explore more about the various CNC machining systems and how programming technology drives fully automated manufacturing processes.
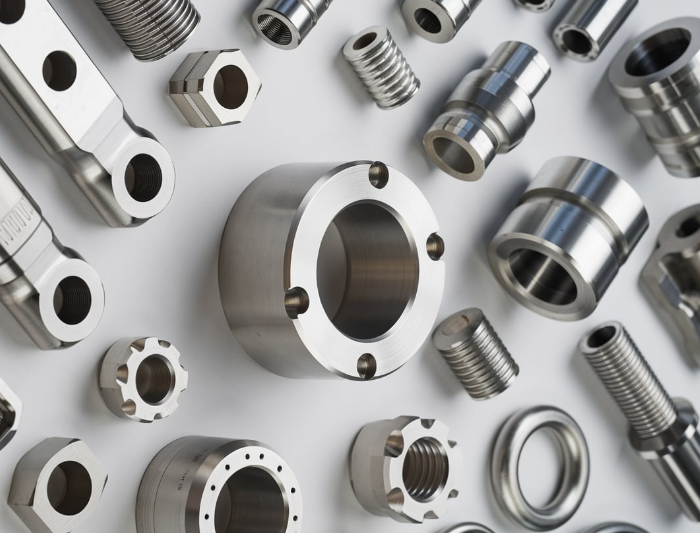
CNC machining capabilities
Our CNC machining workshop is equipped with 20 milling machines (including two milling machine in 5-axis), four lathe machines, and other equipment for drilling as well as EDM machines and quality control tools. We can CNC machine small part, small features, and big parts up to 2 m or 6 in.
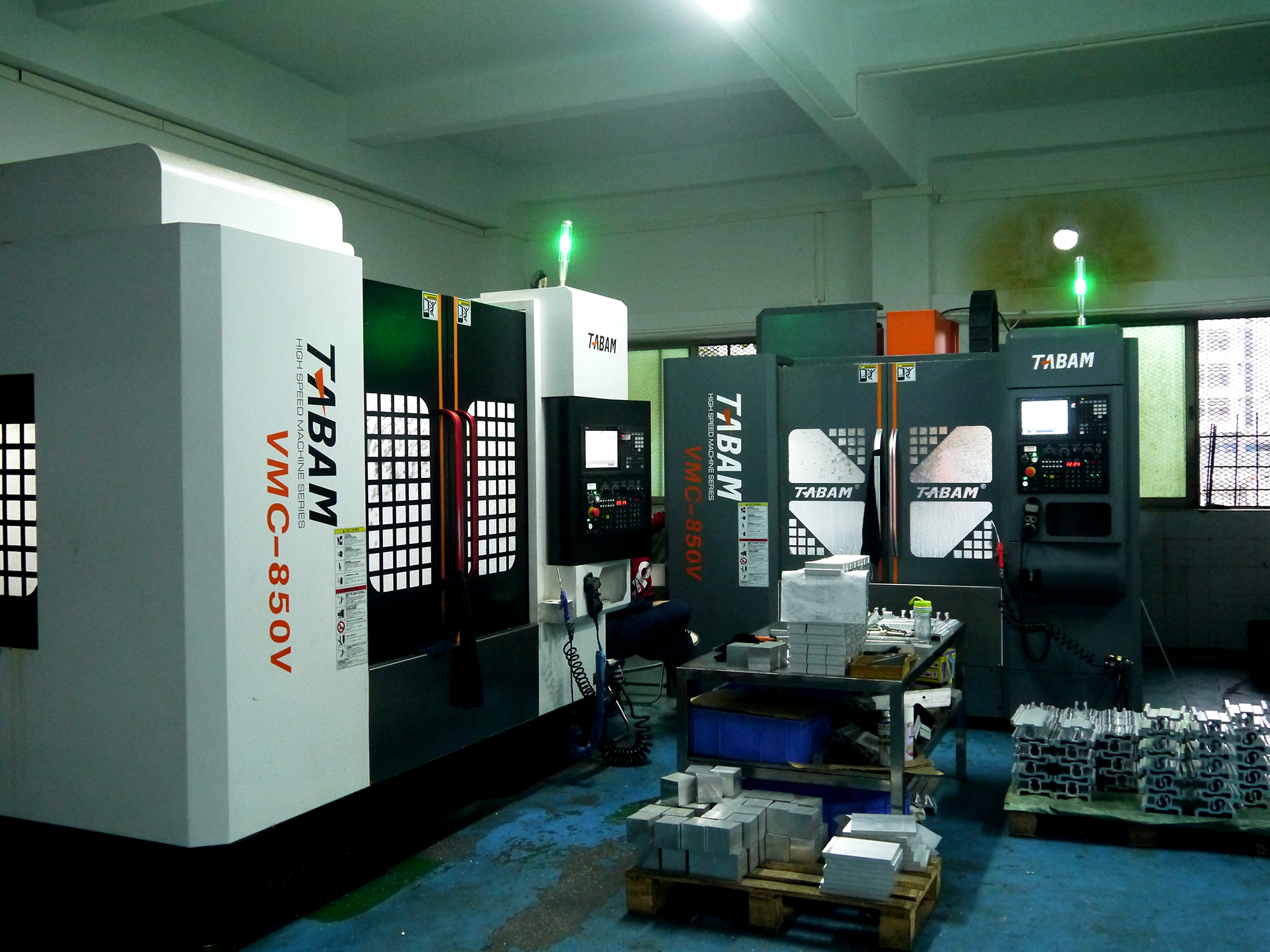
Our CNC Services
CNC Turning
CNC turning is the perfect method for crafting deep holes, threaded features, and diverse cylindrical forms with exceptional surface quality. When you require accurately produced components, quick turnarounds, and flexibility in volume, our CNC turning services at Kintec offer the answer. Discover how we can assist you further.
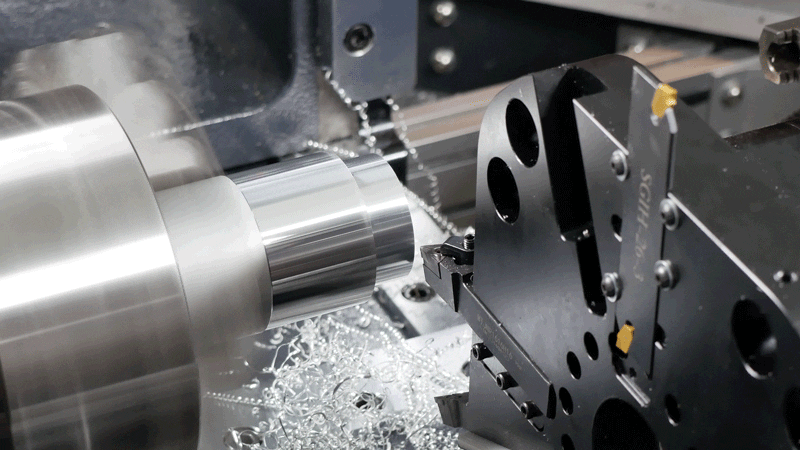
EDM Services
EDM(Electrical Discharge Machining) is a specialized machining process that uses electrical discharges or sparks to remove material from a workpiece. EDM is a versatile method that addresses challenges posed by various materials, shapes, and precision requirements in industries ranging from manufacturing to medical devices and beyond.
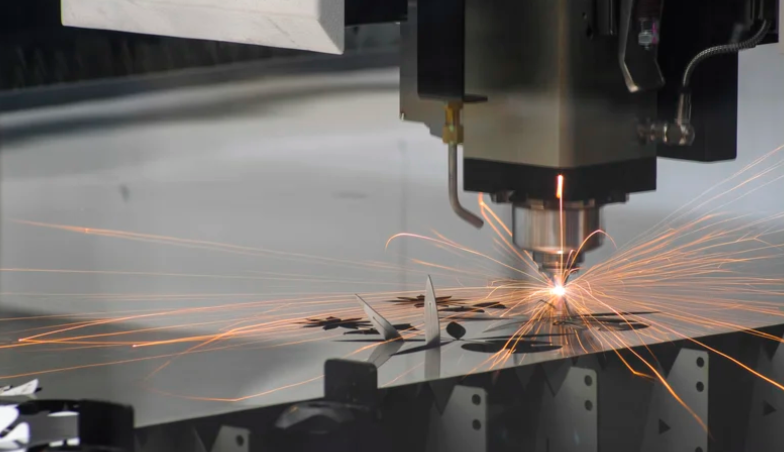
CNC Milling
CNC milling crafts intricate prismatic forms and flat surfaces, catering to a diverse range of commercial and industrial products. Multi-axis CNC machines achieve precision and versatility without fixed tooling. Their design adapts easily to various tasks and shapes, resulting in high flexibility.
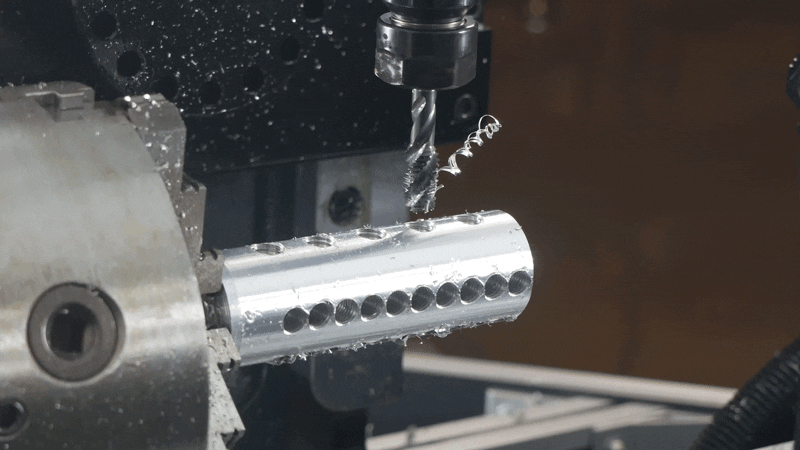
Axis CNC Milling
Our advanced 5-axis CNC machining ensures exceptional precision, complex geometries, and ultra-tight tolerances. Simultaneous multi-angle machining enhances efficiency and surface finishes, delivering superior part quality and dimensional accuracy to meet the highest industry standards.
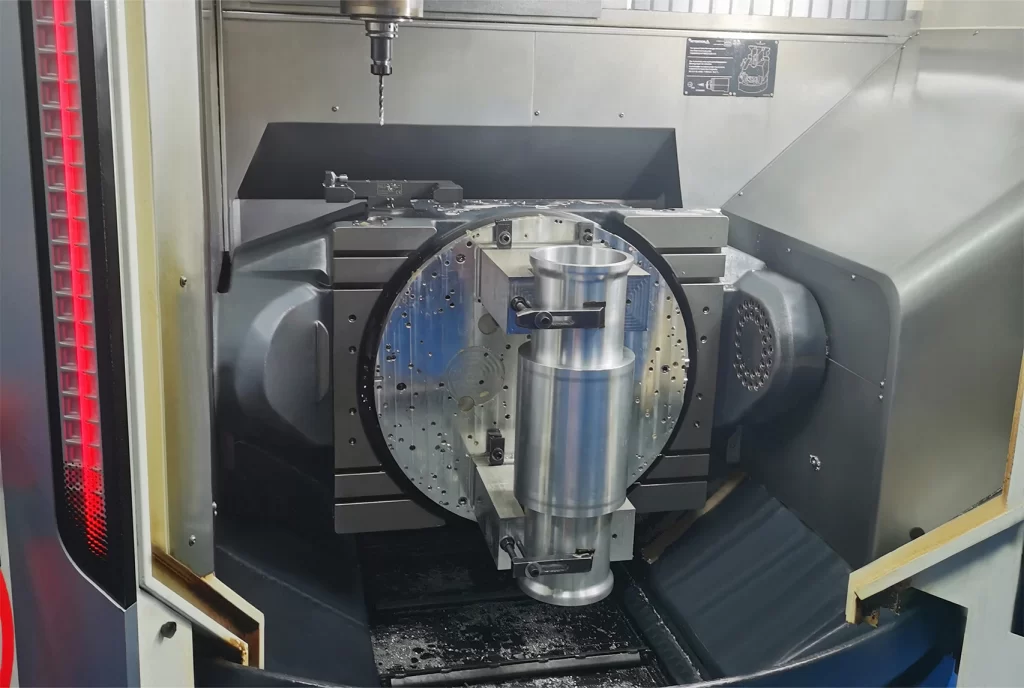
Various materials
Kintec offers precision machining for a wide range of metals and plastics, supporting both prototyping and high-volume production. With expertise in optimizing machining processes, we ensure the most efficient and cost-effective solutions for your parts. Whether you need a single prototype or mass production, upload your CAD files today for a free, expert consultation and quote.
Aluminum
Copper
Options
Brass
Options
Steel
Options
Stainless Steel
Options
Plastic
Options
Tolerance Type | Tolerance Range | Application | Description |
---|---|---|---|
Dimensional Tolerance | ±0.005 mm (±0.0002″) to ±0.1 mm (±0.0039″) | General parts with standard precision | Standard dimensional tolerances, suitable for most general machining tasks. |
Geometric Tolerance | ±0.01 mm (±0.0004″) to ±0.05 mm (±0.002″) | Complex parts needing precise geometry | Controls the form, orientation, location, and runout of features. |
Straightness | 0.005 mm (0.0002″) to 0.02 mm (0.0008″) | Components requiring straight edges | Ensures that a surface or axis is perfectly straight. |
Flatness | 0.005 mm (0.0002″) to 0.03 mm (0.0012″) | Parts needing a flat surface | Ensures the part’s surface does not deviate from the ideal flat plane. |
Cylindricity | 0.01 mm (0.0004″) to 0.05 mm (0.002″) | Cylindrical parts with strict tolerances | Controls the roundness and straightness of cylindrical surfaces. |
Concentricity | 0.01 mm (0.0004″) to 0.03 mm (0.0012″) | Parts where concentricity is crucial | Ensures that features (e.g., holes, shafts) are aligned within a common centerline. |
Perpendicularity | 0.01 mm (0.0004″) to 0.05 mm (0.002″) | Parts needing precise perpendicular surfaces | Ensures that features are exactly perpendicular to each other. |
Our Machining Tolerance Standard
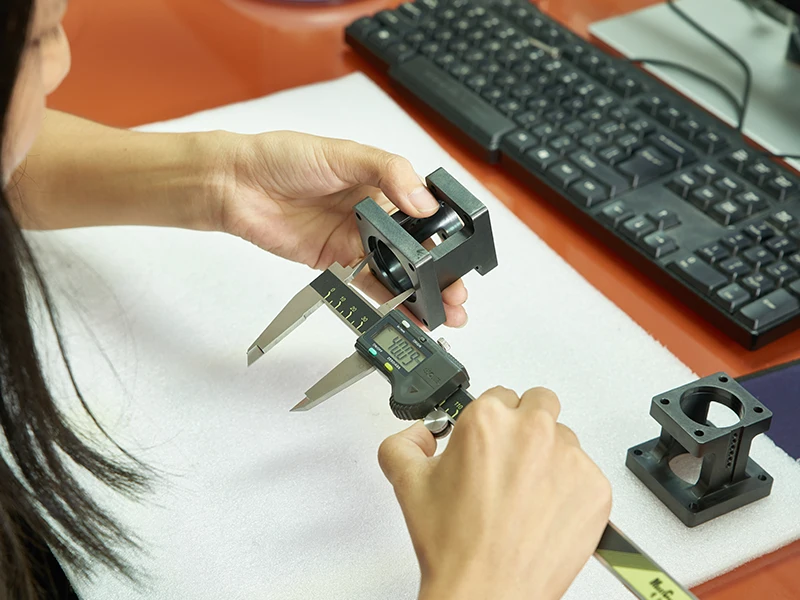
This table presents our recommended tolerance standards. If no specific tolerance requirements are provided, we will proceed with machining according to the standard class. Our team will also reach out to discuss your product’s specific needs and recommend appropriate tolerances based on our expertise and industry experience