3D print your creativity
3D Printing Service | The Ultimate Additive Manufacturing
Main 3D Printing Services At Firstmold
As the name suggests, rapid prototyping involves the swift production of one or a few parts at the start of a project. To achieve fast and cost-effective prototyping, we utilize four advanced technologies: CNC machining, rapid tooling, 3D printing, and urethane casting. For details on our CNC machining and rapid tooling services, please refer to the respective pages. Below is an overview of our 3D printing and urethane casting capabilities.
- Rapid turnaround times
- Enables concurrent manufacturing of multiple parts
- Accessible technology for startups and small businesses
Design Guidelines for 3D Printing Techniques
3D printing part sizes:
FDM | 200 x 200 x 200 mm for desktop printers, up to 900 x 600 x 900 mm for industrial printers |
SLA | 145 x 145 x 175 mm for desktop printers, up to 1500 x 750 x 500 mm for industrial printers |
DMLS/SLM | 250 x 150 x 150 mm, up to 500 x 280 x 360 mm |
SLS | 300 x 300 x 300 mm, up to 750 x 550 x 550 mm |
MJF | 380 x 285 x 380 mm |
Supports in 3D printing
Supports are a type of structure of a part, that can help to prevent deformation and secure the part to the printing bed during the 3D printing process. Can you print without supports and when do you need that? Yes, you can 3D print without support. Take the FDM 3D printing as an example, when a feature is printed with an overhang of more than 45 degrees, it may sag enough to destroy the part, at this point you need a support structure. In another case, bridging allows parts to be printed without the use of support material and with minimal sag because hot materials can be stretched out. But if the bridge is longer than 5 mm and you need a good surface finish, a support structure is required. In addition, SLA and DLP 3D printers generally use supports.
Part orientation in 3D printing
Another critical parameter in 3D printing manufacturing is the part orientation, which refers to the way in which the part is in contact with the build plate, it has an impact on the accuracy, time, strength, and surface finish of a 3d printed product. The best build orientation would be different in various examples, however, here are some tips that may be helpful for choosing the way of the part orientation.
- Find the face that can provide the best adhesion to the build plate and the highest stability.
- If the product needs to be subject to stress, then it should be oriented to ensure the direction of the minimum applied stress is parallel to the build direction, which is usually the vertical direction.
- Be clear about the build volume of the 3D printer.
- FDM prints are easier to delaminate and fracture in the Z direction than in the XY direction when subjected to tension.
- Orient the part to make overhangs of less than 45° are minimized.
- In the vertical direction, cylindrical features print more precisely than in the horizontal.
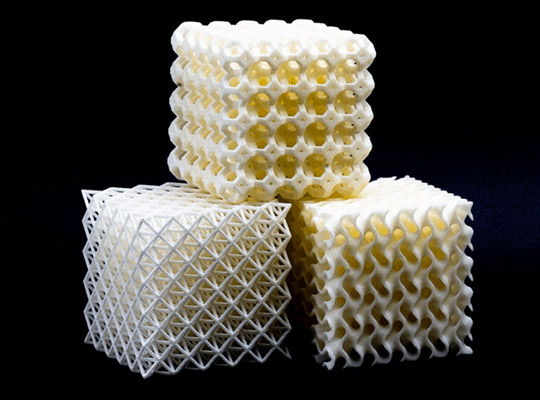
Dimensional accuracy in 3D printing
The dimensional accuracy refers to how accurate the size and form of the printed part are compared to that in the CAD design. Factors that affect dimensional accuracy include material quality, equipment, post-processing, and more. Dimensional tolerance, shrinkage, and support requirements are three key elements to measuring dimensional accuracy. Below are the dimensional tolerance of different 3D processes.
FDM dimensional tolerance | prototyping (desktop):±0.5% (lower limit:±0.5 mm), industrial:±0.15% (lower limit:±0.2 mm) |
SLA dimensional tolerance | prototyping (desktop):±0.5% (lower limit:±0.10 mm) industrial:±0.15% (lower limit:±0.01 mm) |
SLS/MJF dimensional tolerance | ±0.3% (lower limit:±0.3 mm) |
3D Printing Plastic Materials Guide
ABS | Tough, strong, durable, heat-resistant, cost-effective, flexible, reusable, not biodegradable | Car bodies, appliances, and mobile phone cases |
PLA | Easy to work with, environmentally friendly, biodegradable, available in resin and filament with a variety of colors | Food packaging, biodegradable medical devices and implants |
PVA | Water-soluble | Often use to create a support structure for portions of a product that may warp or collapse |
PP | Affordable, chemical resistant, flammable, and degrades with UV light | Household containers, lab equipment, and textiles |
Nylon/PA | Strong, lightweight, durable, heat and impact-resistant, but not resistant to strong acids and bases | Applications that require high mechanical properties and functional prototypes |
PEI | Can withstand high heat | Injection mold tools and heat-resistant components |
PC | Heat resistant up to 135 °C, durable, impact and shatter resistant, moderately flexible, transparent, electrically non-conductive | Prototype windows and other clear products |
PMMA/Acrylic | Good impact strength, comparable clarity, and UV absorption properties | Automobile headlights, commercial aquariums and other alternatives to glass |
CPVC | High heat distortion temperature, chemical inertness, dielectric, and flame and smoke properties | Chemical processing, power generation, semiconductor, wastewater treatment |
PEEK | Wear-resistant, good weight-to-strength ratio, high thermomechanical properties | Medical custom-made implants, devices, aerospace and automotive parts |
PETG | High impact resistance, excellent chemical and moisture resistance | Compliant mechanisms, water bottles, electronic enclosures |
TPU | Flexible, abrasion-resistant, resistant to impacts and many chemicals | Sporting goods, aerospace and automotive |
PETP/Ertalyte | High dimensional stability, mechanical strength, low moisture absorption, physiologically inert | Thin films, containers for liquid drinks |
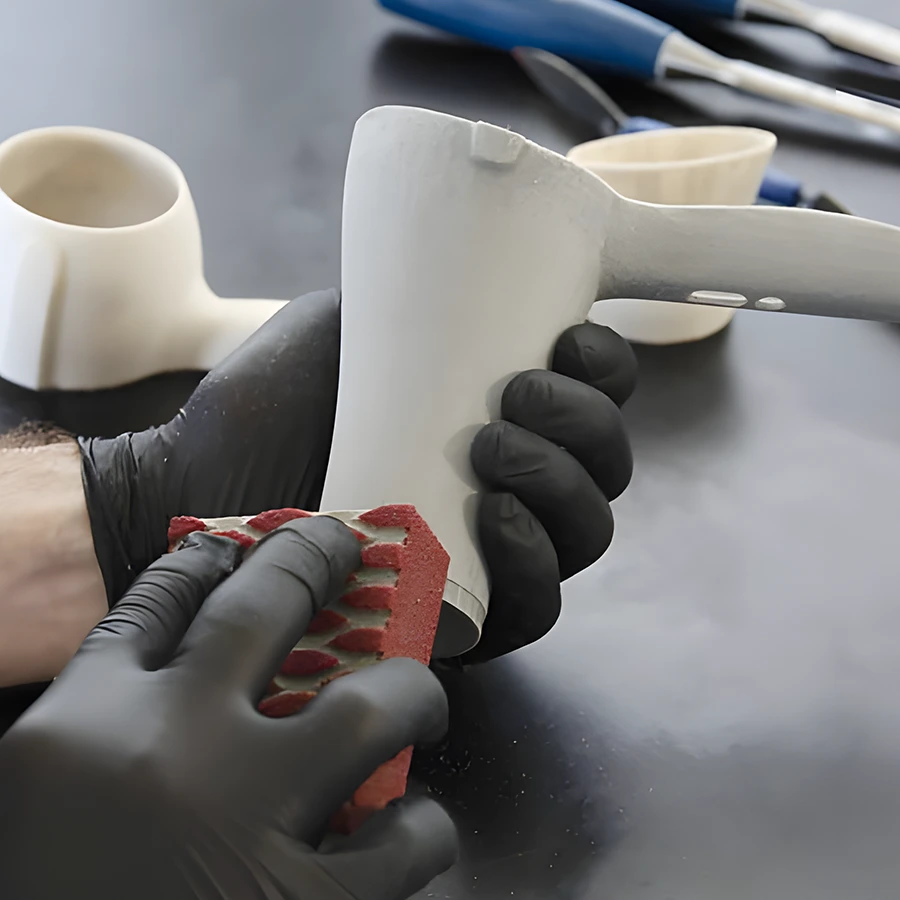
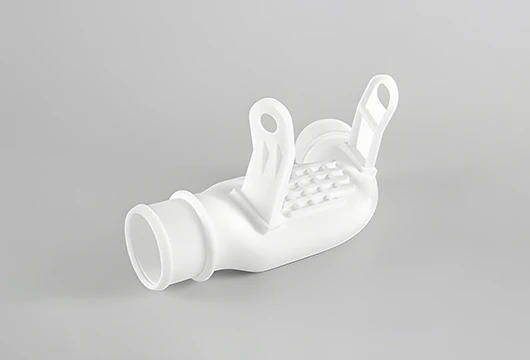
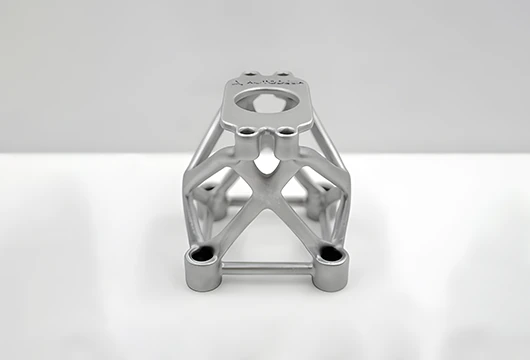
3D printing surface treatment
3D printing surface treatment refers to the process of forming a layer on the surface of 3D printed products that has different mechanical, physical, and chemical properties. The main purpose of 3D printing surface treatment is to meet the requirements of the product’s corrosion resistance, wear resistance, decoration, or other special functions.
Common 3D printing surface treatment methods include sanding, polishing, sandblasting, painting, etc.