High-Quality, Cost-Effective Aluminum CNC Machining – Precision CNC Aluminum Parts
Are you in search of a reliable provider for rapid-turn aluminum CNC machining services and precision-manufactured CNC products? Leveraging a diverse fleet of advanced CNC machines, our superior design and production capabilities ensure the delivery of top-grade OEM aluminum CNC machined parts to clients worldwide.At mazaro – a leading CNC machining supplier in China – we offer comprehensive, certified CNC machining processes for aluminum, including milling, turning, and drilling. Our services are ideally suited for rapid prototyping and low-volume production of both end-use components and complete assemblies.
Advantages and Applications of Aluminum in CNC Machining
Aluminum is a pivotal industrial material, extensively utilized in CNC machining due to its exceptional thermal properties and outstanding machinability. These characteristics make it a preferred choice across various manufacturing sectors. One primary reason engineers opt for CNC machined aluminum parts is the material’s excellent machinability, allowing for efficient and precise fabrication. This advantage benefits not only manufacturers but also businesses procuring these components and the end-users who rely on high-quality aluminum products.
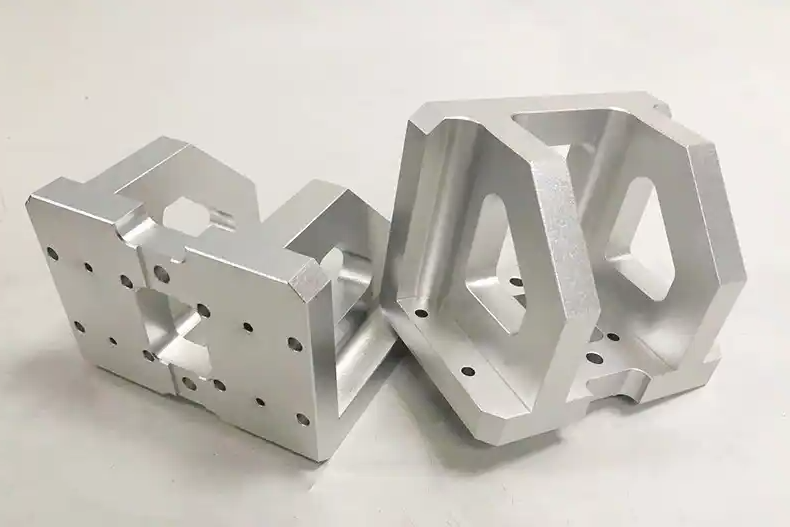
Aluminum Material Benefits:
⒈ Lightweight & High Strength-to-Weight Ratio: Aluminum’s low density and excellent strength make it ideal for applications where weight reduction is critical.
⒉ Superior Machinability: Its soft, tractable, and malleable nature allows for precise and efficient CNC machining.
⒊ Durability & Corrosion Resistance: Aluminum withstands harsh environments and resists corrosion, ensuring long-lasting performance.
⒋ Safety & Versatility: Being non-magnetic and non-flammable, it offers additional safety benefits. Its anodization potential allows for varied surface finishes.
⒌ Thermal & Electrical Properties: Aluminum performs well in low temperatures and provides high electrical conductivity.
⒍ Eco-Friendly: Its recyclability supports sustainable manufacturing practices.
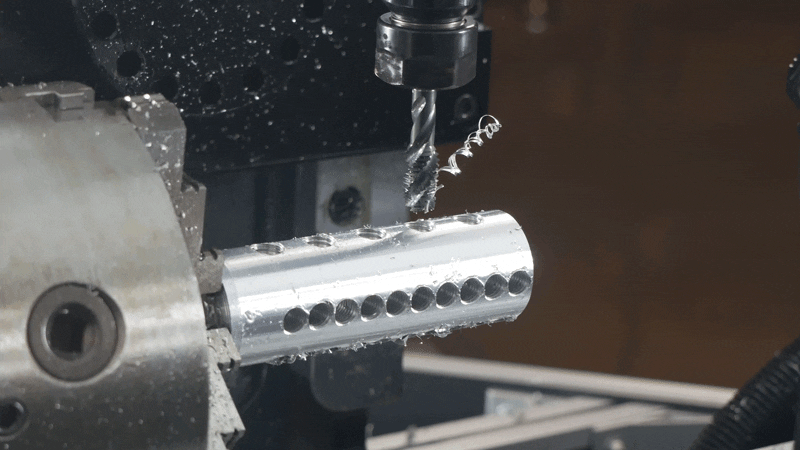
Your Trusted Partner for Custom CNC Aluminum Machining Solutions
As a leading CNC machining manufacturer in China, we possess a dedicated team of technical experts and management professionals capable of designing custom components based on your drawings and samples. Our extensive experience and in-depth understanding of various aluminum material properties enable us to provide optimal machining solutions tailored to your specific requirements.
Overview of Our Precision Aluminum CNC Machining Services
We offer an extensive selection of aluminum materials for CNC machining, each with unique properties to suit diverse application requirements:
Aluminum 6061: Known for its excellent mechanical properties, weldability, and versatility, making it ideal for structural components.
Aluminum 2024: Renowned for high strength and fatigue resistance, commonly used in aerospace applications.
Aluminum 5052: Noted for its superior corrosion resistance, particularly in marine environments, and good formability.
Aluminum 6063: Often referred to as an architectural alloy, it offers high-quality surface finish and is commonly used in intricate extrusions.
Aluminum 7050: Provides high strength and stress corrosion resistance, suitable for aerospace structural components.
Aluminum 7075: Features exceptional strength-to-weight ratio and is extensively used in high-stress applications such as aircraft and marine structures.
Aluminum MIC-6: A cast plate known for its stability and flatness, ideal for precision machining applications.
Surface treatment process for aluminum parts
We offer a comprehensive suite of surface finishing services to enhance the performance and aesthetics of your components:
Abrasive Blasting:
- Sand Blasting: Utilizes fine grains of sand propelled at high velocity to clean and texture surfaces, improving paint adhesion.
- Shot Blasting: Employs spherical media to remove surface contaminants and impart compressive stress, enhancing fatigue resistance.
Polishing: Achieves a smooth, reflective surface by mechanically refining the material, enhancing both appearance and functionality.
Anodizing: An electrochemical process that thickens the natural oxide layer on aluminum parts, increasing corrosion resistance and allowing for dyeing to various colors.
Chemical Treatments:
- Oxidation: Forms a protective oxide layer on metals to prevent further corrosion.
- Chromate Conversion Coating: Applies a chromate layer to enhance corrosion resistance and paint adhesion, commonly used on aluminum alloys.
Electrophoresis (E-Coating): Deposits a uniform, thin coating onto conductive surfaces using an electric field, providing excellent corrosion protection and a smooth finish.
Powder Coating: Applies a dry powder to the surface, which is then cured under heat to form a hard, durable finish, offering both aesthetic appeal and protection against environmental factors.
Painting: Applies liquid paint to the surface for aesthetic purposes and additional protection against corrosion and wear.

Aluminum CNC Machining Applications
Aluminum CNC machined components find extensive applications across various industries due to their unique properties:
Aerospace Industry: Utilized in aircraft structures and components for their lightweight and durable characteristics.
Automotive Sector: Employed in engine and suspension systems to enhance performance and fuel efficiency.
Medical Field: Applied in medical devices and implants owing to aluminum’s biocompatibility and sterilization capabilities.
Marine Industry: Integrated into shipbuilding due to their corrosion resistance and lightweight nature.
Electronics Industry: Used in electronic components for effective thermal management and structural support.
Agricultural Machinery: Incorporated into farming equipment for durability and resistance to harsh environments.
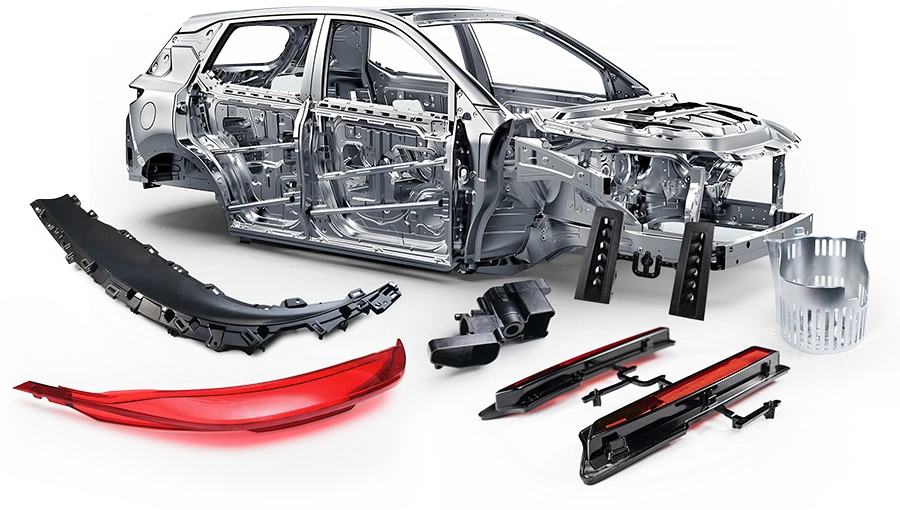